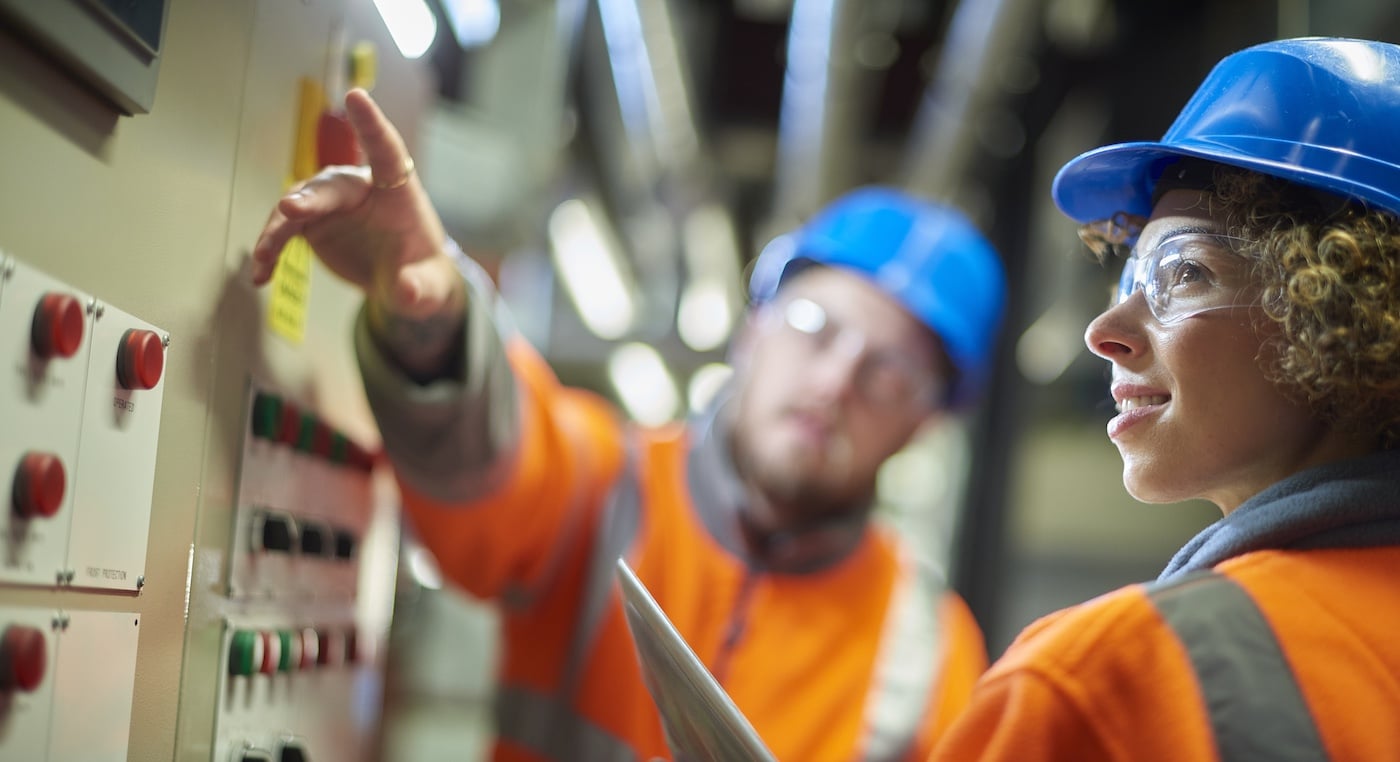
Die Welt ist übersät mit Kunststoffabfällen. Allein im Vereinigten Königreich werden jährlich über 5 Millionen Tonnen Kunststoff verwendet, von denen nur 20-25 % wiederverwertet oder recycelt werden. Der Großteil dieses Recyclinganteils entfällt auf Thermoplaste, die mehrfach eingeschmolzen und wiederverwendet werden können. Duroplaste wie Polymere und Kunststoffe auf Epoxidbasis können dagegen nach dem Aushärten nicht mehr in ihre Bestandteile zerlegt werden und landen weiterhin auf der Mülldeponie.
Das ist nicht nur schlecht für die Umwelt, sondern auch schlecht fürs Geschäft, da die Kosten für die Deponierung und die Abfallsteuern weiter steigen. „Going Green“ ist nicht mehr nur ein vage angenehmes Konzept, sondern bringt echte finanzielle Vorteile mit sich und ist für die Industrie, die etwa ein Drittel aller Deponieabfälle verursacht, ein immer wichtigerer Faktor bei der Vergabe von Bauaufträgen.
Ein bahnbrechender Hersteller hat eine neue Technologie entwickelt – das Pulver-Abformverfahren („Powder Impression Moulding“, PIM) – mit der unerwünschte vermischte Polymerabfälle zu leistungsstarken, umweltverträglichen Platten verarbeitet werden können.
Dabei handelt es sich um strapazierfähige, glatte und vielseitige Platten, die sich für eine Vielzahl von Anwendungen im Bauwesen und darüber hinaus eignen. Sie sind als Alternative zu importiertem Sperrholz oder zu neuen Kunststoffplatten konzipiert, können aber am Ende ihrer Lebensdauer vollständig recycelt werden. Tatsächlich behauptet der Hersteller, dass das Produkt nicht nur eine umweltfreundliche Alternative zu Sperrholz ist, sondern sogar ein überlegenes Produkt, da es ähnliche technische Eigenschaften wie Sperrholz aufweist, jedoch verrottungssicher ist, sich vor Ort leicht zuschneiden lässt, ohne zu splittern oder Staub zu verursachen, Farbe länger und gleichmäßiger hält und sich leicht mit Schrauben befestigen lässt.
Wie zu erwarten ist, ist es in der Anschaffung etwas teurer als Sperrholz (ca. 10 %), aber die gesamtlebenskosten machen das wieder wett, da das Produkt aufgrund seiner Langlebigkeit eine wesentlich längere Lebensdauer hat und immer wieder recycelt werden kann. Und das sogar mehrmals!
Da es sich bei der PIM-Technologie um ein völlig neues Verfahren handelte, hat Babcock Wanson UK von Anfang an mit dem Hersteller zusammengearbeitet. Babcock Wanson hat den gesamten Heiz- und Kühlprozess für den Betrieb des PIM-Systems auf der Grundlage seines EPC2000 ES Wärmeträgerheizers entworfen und gebaut. Der Produktionsprozess wird mit pulverisierten Mischkunststoffabfällen gespeist und erfordert eine Erwärmung nach einem festgelegten Profil, um den Kunststoff zu schmelzen, der dann für einen bestimmten Zeitraum auf einer genau kontrollierten Temperatur gehalten und anschließend nach einem festgelegten Profil wieder abgekühlt wird, um ein perfektes Produkt zu gewährleisten.
Der Wärmeträgerheizer EPC2000 ES mit integriertem Abgas-Verbrennungsluft-Wärmetauscher wurde aufgrund seiner hohen Gesamtbetriebseffizienz und Gesamtleistung ausgewählt, die den Prozessbedarf problemlos erfüllt. Der EPC2000 ES ist ein vertikal befeuerter Heizer, der aus durchgehenden konzentrischen Spulen mit einer Verbrennungskammer mit Flammenumkehr und drei Gasdurchläufen besteht. Die doppelte Verbrennungsluftvorwärmung sorgt für eine hohe Verbrennungseffizienz von bis zu 92 %, während die komplette Isolierung der Außenhülle für minimale Wärmeverluste sorgt.
Das Wärmeträgersystem wurde mit einem separaten Kühlkreislauf (obwohl dieselbe Flüssigkeit verwendet wird) unter Verwendung von Luftkühlern konzipiert, die jeweils mit zwei axialen Kühlventilatoren ausgestattet sind, um die Kühllast bereitzustellen.
Zehn unabhängige Einheiten zur Temperatursteuerung wurden an die Heiz- und Kühlverteilungsleitungen angeschlossen, um die heiße und kalte Flüssigkeit automatisch zur Produktionslinie zu leiten, sodass sich jeder Teil der Linie zu jedem Zeitpunkt in einem anderen Teil des thermischen Zyklus befinden kann; ein entscheidender Faktor für das benötigte Fließband-Produktionssystem.
Der EPC2000 ES und das Kühlsystem bedienen derzeit eine Produktionslinie, bieten aber Kapazität für eine zweite. Die Produktion kann durch zusätzliche Heiz- und Kühlkapazitäten erweitert werden, wenn die Produktion steigt, um die Nachfrage zu decken.
Eine der größten Herausforderungen für Babcock Wanson bei dieser Installation bestand darin, ein einziges Wärmeträgermedium zu finden, das sowohl zum Heizen als auch zum Kühlen der Formen geeignet ist. Babcock Wanson hat weltweit recherchiert und thermodynamische Modelle genutzt, um geeignete Flüssigkeiten auszuwählen.
You must be logged in to post a comment.