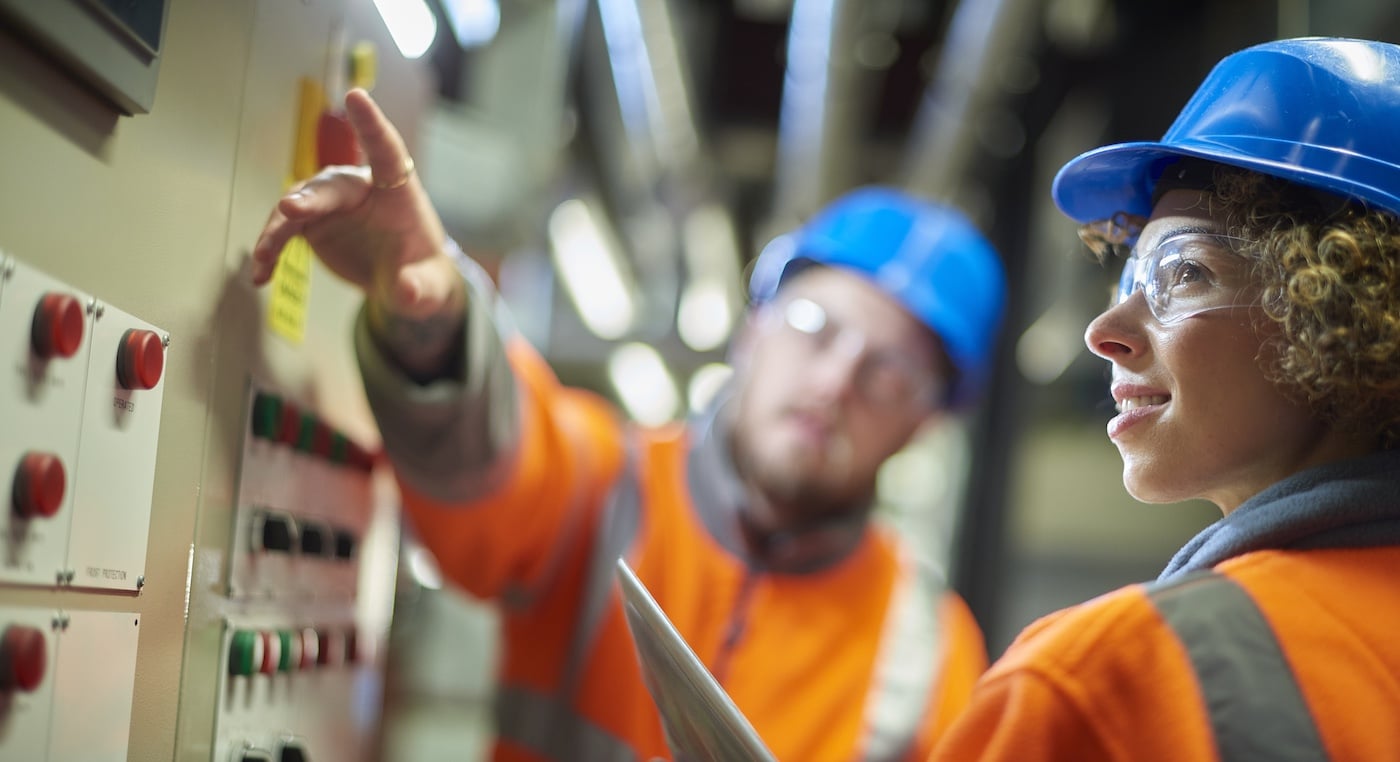
The world is littered with waste plastics. The UK alone uses over 5 million tonnes of plastic per annum, with just 20-25% recovered or recycled. The vast majority of this recycling figure applies to thermoplastics which can be repeatedly melted down and re used. Thermosets such as Polymers and Epoxy based plastics, on the other hand, cannot be separated back into their constituent elements once cured and continue to head for landfill.
Clearly bad for the environment, landfill is also bad for business as landfill costs continue to rise, along with taxes on waste. ‘Going green’ is no longer a vaguely pleasant concept, but has genuine financial benefits and, for the construction industry that generates about one third of all landfill, is an increasingly important factor in winning construction tenders.
One ground breaking manufacturer developed a new technology – Powder Impression Moulding (PIM) – which takes unwanted co-mingled polymer waste and re-manufactures it into high-performance, environmentally sustainable panels.
These panels are hard-wearing, smooth-faced, versatile boards suitable for a variety of applications in construction and beyond. They are engineered to perform as an alternative to imported plywood or to virgin plastic panels, yet in turn are fully recyclable at end-of-life. In fact, the manufacturer claims that the product is not just an environmentally friendly alternative to plywood but is actually a superior product as it has similar technical properties to plywood, but is rot proof, easy to cut on site with no splintering or dust, holds paint longer and more evenly and can be readily fixed with screws.
As you might expect, it’s slightly dearer than plywood for the initial outlay (about 10%), but life time costs more than make up for that as the product’s durability means it has a considerably longer life span and can be recycled again and again. And again for that matter!
As the PIM technology was a completely new process, Babcock Wanson UK worked with the manufacturer from its inception. Babcock Wanson designed and built the entire heating and cooling process to operate the PIM system based around its EPC2000 ES Thermal Fluid Heater. The production process is fed with pulverised waste mixed plastics and requires heating following a fixed profile to melt the plastic, held at a close control temperature for a period and then cooled at a fixed profile to ensure a perfect product.
The EPC2000 ES Thermal Fluid Heater with integral exhaust gas to combustion air recuperator was selected due to its high overall operating efficiency and total output easily meeting the process demand. A vertical fired heater, the EPC2000 ES is constructed from continuous concentric coils with flame reversal combustion chamber and three gas passes. Its double combustion air preheating provides high combustion efficiency of up to 92% whilst its complete insulation of the external shell ensures minimal heat loss.
The thermal fluid system has been designed with a separate cooling circuit (although using the same fluid) using air blast coolers, each fitted with two axial cooling fans to provide the cooling load.
Ten independent Temperature Control Units have been connected to the heating and cooling distribution mains to automatically feed the hot and cold fluid to the production line, meaning that each part of the line can be at a different part of the thermal cycle at any given time; a key factor for the flow line production system needed.
The EPC2000 ES and cooling system currently operates one production line but has capacity for a second. Further production can be added with additional heating and cooling capacity being simply added as production ramps up to meet demand.
One of the key challenges for Babcock Wanson in this installation was to source a single fluid capable of both heating and cooling the moulds. Babcock Wanson researched worldwide and used thermodynamic modelling to select suitable fluids.
You must be logged in to post a comment.