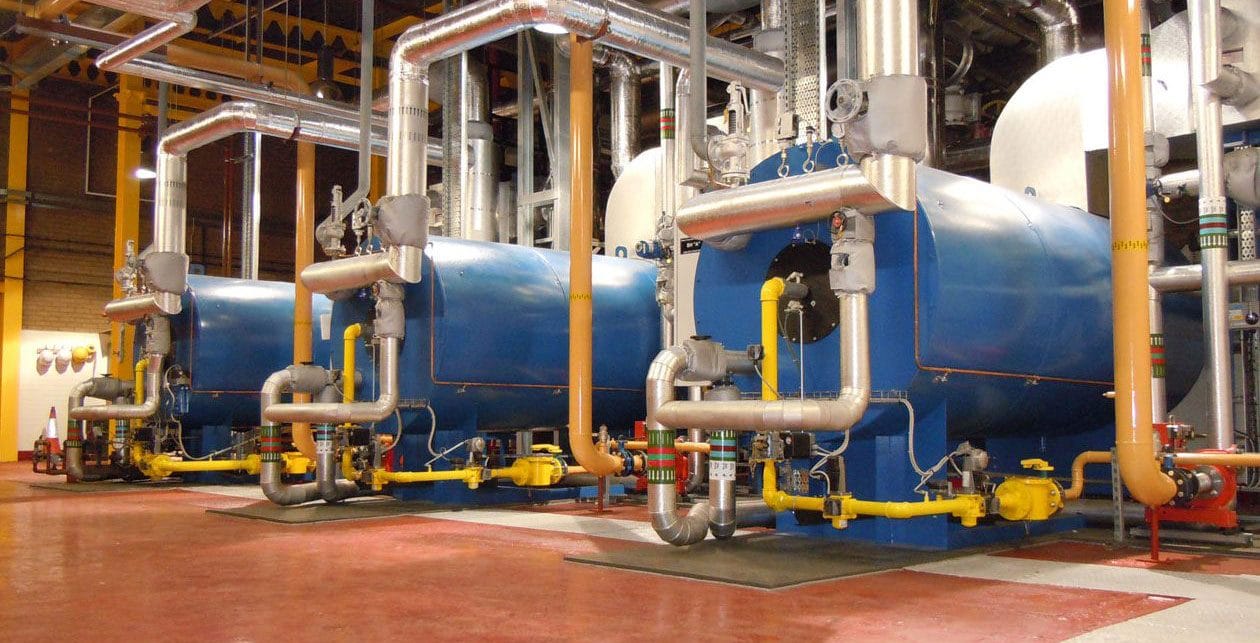
With the NHS aiming to reduce its 2007 carbon footprint by 10% by 2015, we look at how one NHS Trust has approached the subject and considerably reduced its carbon emissions by refurbishing its boiler house and moving from oil to gas fired steam generation.
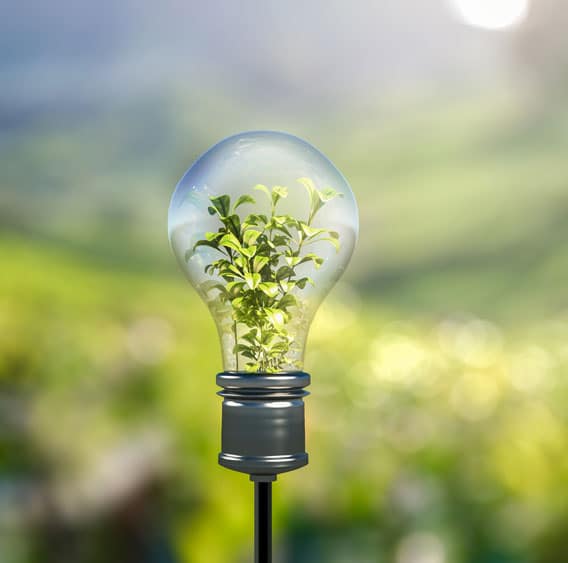
Carbon Reduction Commitment (CRC)
In the current climate – both financial and environmental – energy saving is a major priority for any organisation. Reducing your Carbon Footprint is no longer just a vague concept that is seen as a good bit of PR; it is now financially savvy and driven by schemes such as the Carbon Reduction Commitment (CRC), which is likely to affect around 5,000 of the UK's largest organisations, including the NHS.
Under the CRC scheme, any organisation whose half hourly electricity consumption totals more than 6,000 MWh per year (currently equivalent to approximately £500,000 PA) will be required to record all energy usage (other than transport fuels), including electricity, gas and oil. From 2012, they will then be faced with a tax on the carbon they emit.
There’s no surprise that the NHS falls under the CRC scheme; it is, after all, a major user of energy. However, unlike many other organisations which seem to have adopted a head in the sand approach, the NHS has been proactive in investigating Carbon reduction using expert advice and feedback from members. The resulting Department of Health’s Sustainable Development Strategy was published in 2008 and the NHS Carbon Reduction Strategy for England early in 2009. Within the latter document, the NHS was identified as having a carbon footprint of about 18 million tonnes of CO2 per year, composed of energy (22%), travel (18%) and procurement (60%).
Bedford Hospital NHS Trust is a good case in hand.
Despite an increase in efficiency, the NHS has increased its carbon footprint by 40% since 1990. To meet the Climate Change Act’s targets of 26% reduction by 2020 and 80% reduction by 2050, the NHS will have to work hard; it aims to reduce its 2007 carbon footprint by 10% by 2015. It’s not an easy task, that’s for sure. And what makes it all the more difficult is the differing nature of Trust’s across England, whose buildings and plant vary widely in terms of age and efficiency.
Even with strategic guidelines in place, each Trust still has its own decisions to make on areas to target for maximum carbon and efficiency savings. With procurement representing approximately 60% of a Trust’s carbon footprint, you would be excused for thinking this is the likely area to prioritise, but this may not necessarily be the best step forward. You may be better off looking at energy consumption as the most efficient means of reducing your carbon footprint.
Bedford Hospital was one of the NHS Trusts that was quick to react to the CRC proposals, with the Estates Team evaluating the impact on the Trust. It concluded the scheme will require the Trust to pay a tax of circa £12/tonne of carbon produced by the Trust as a direct result of the utilities used on the main site. It is currently estimated the Trust produces around 9000 tonnes of carbon a year, equal to an additional cost of £108,000 per year.
Working with carbon reduction specialists, Bedford Hospital identified a number of areas ripe for efficiency improvements, with the boiler house being the priority.
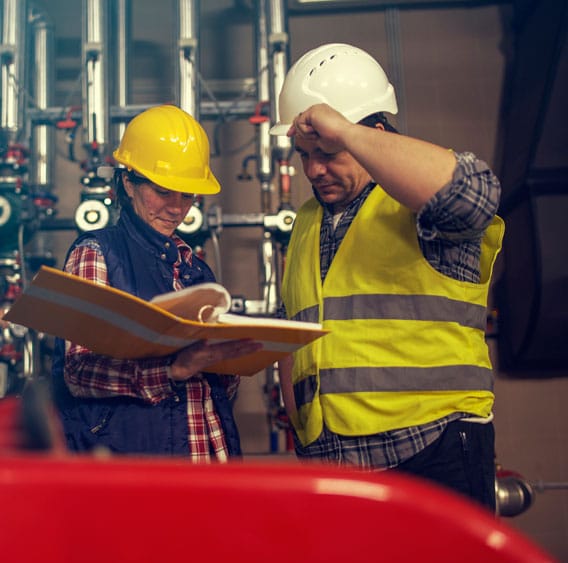
Partly Funded by Government Scheme
The complete refurbishment of the boiler house was part funded by a Government scheme, which required the Trust to clearly establish the CO2 emissions reduction. Bob Fairclough, Senior Estates Engineering Manager at Bedford Hospital, worked closely with the chosen contractor Leemoll Services and Consulting Engineer Hoare Lea for the job and selected Babcock Wanson as the boiler supplier, which was able to furnish the Trust with detailed figures on the carbon savings made by switching to their energy efficient automated sequence control coil steam generators operating on gas. The figures were studied carefully, with Bedford Hospital estimating the conversion to gas will reduce its carbon footprint by 1500 tonnes per year, while also providing improved efficiency – and security - on site for the Trust’s main heating source. NHS.
An experienced Project Manager was also employed to oversee the refurbishment and ensure the hospital’s steam supply was maintained throughout. As a critical steam user, the hospital could not permit their steam supplies to be out of action at any time, which resulted in a phased boiler replacement process. Carefully planned, the replacement ran very smoothly and didn’t require the Trust to hire temporary boilers during the work, which would have been costly and disruptive to the operation of the site.
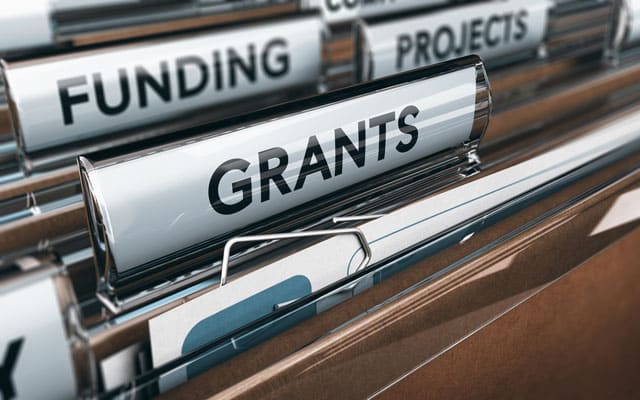
The Solution
The four heavy oil fired Firetube Boilers have now been replaced with three Babcock Wanson 2500kg/h ESM Steam Generators fitted with high efficiency exhaust gas economisers. These new units use coil type steam generator technology giving operating efficiencies of around 94% and low emissions. The Babcock Wanson Steam Generators utilise modern controls to maintain a close ratio between the burner firing rate and water input. This ensures close control of both steam output and steam quality. The burner can be supplied to use different gaseous or liquid feeds, but at Bedford Hospital the primary fuel is gas, with one unit configured for dual fuel operation (gas or oil) as a precautionary measure against gas supply failure.
The benefits of using high efficiency steam generators not only include energy consumption and carbon emissions but also improved safety (the chance of a pressurised water explosion is virtually eliminated), simplicity of control, compact size (they take about half the footprint of the previous fire tube boilers) and they are considerably quieter, cleaner and cooler in operation, making the boiler house a far nicer environment in which to work. In fact, the new boiler house is almost impossible to recognise from its former incarnation; it’s a very modern, spacious, bright space.
During the winter two of the ESM Steam Generators will operate full time, with the third acting as a stand-by; this goes down to one in summer with reduced heating demands. The stand-by unit can be fired up very quickly – it takes no more than 15 minutes to start generating steam from cold - when the need arises and this is performed automatically through the use of a purpose designed sequence control panel to which the steam generators are linked. With the former incumbents, four hours to generate steam from cold was standard, meaning the stand by boiler had to be in continual operation to avoid the risk of losing steam to the hospital – hardly efficient.
In addition to the ESM Steam Generators, two Babcock Wanson 1200kg/h VPX vertical coil type Steam Generators have been installed in the new Sterilisation Services Department building, for use in sterilisation processes.
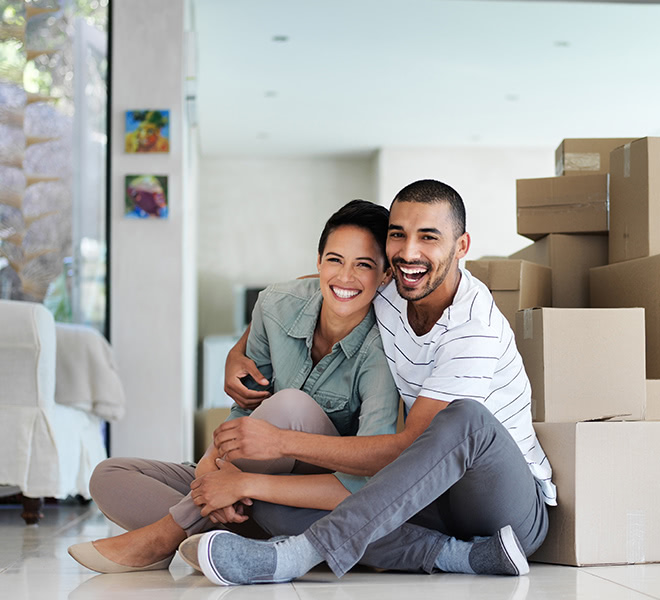
What the Client Thought
The boiler house refurbishment was largely completed in summer 2010 and a full review of savings achieved will be carried out around 12 months from that time frame. With all the investigative work done prior to the installation, the Trust believes the figures will be impressive. In its Annual Report 2009/10, it states: “A major carbon footprint reduction will be achieved when the scheme currently in progress to change the main boiler fuel from heating oil to gas is completed in summer 2010. This £900k project will reduce our carbon emissions via energy usage by around 15% by removing the need to use heavy fuel oil, as the new boiler plant will use natural gas as its main fuel source.”
Bedford Hospital Trust has a proactive and positive attitude to reducing its carbon footprint. It researched the options and possible funding initiatives and put a good team of people together, from inside and outside the Trust, who worked closely together to achieve the smooth transition to a new, efficient steam generation system. It has certainly made a stride towards the NHS’ overall 10% carbon reduction set for 2015. Could other Trust’s follow suit?
Testimonianze dei clienti
— Sam Robinson, Responsabile della progettazione e della manutenzione degli impianti, Gurit Composite Components"I riscaldatori sono ben costruiti, di facile manutenzione e vantano prestazioni ottimali. Una delle unità presenti in loco è rimasta in funzione pressoché 24 ore su 24, 7 giorni su 7, per 360 giorni, facendo rilevare un solo guasto in otto anni. I comandi sono diretti, senza aggiunte complesse o superflue, e sono realizzati in modo da consentire lo svolgimento delle attività necessarie e garantire un corretto funzionamento."
Andrew Taylor, Direttore, Freedom Brewery"Abbiamo scelto il fluido termico perché è più economico da installare e da utilizzare, ha un ingombro minore rispetto al vapore e offre una soluzione più ecologica."
Duncan McLeod, Responsabile della progettazione, Total Bitumen Preston"Tra i principali vantaggi offerti dai riscaldatori EPC troviamo una riduzione dei costi del combustibile e delle emissioni del camino, una maggiore efficienza e il passaggio dal combustibile pesante al gas naturale, che ha eliminato la necessità di stoccaggio del combustibile in loco."
Jeff Farey, Responsabile della manutenzione, Beardow Adams"I riscaldatori Babcock Wanson si sono dimostrati affidabili in ambito aziendali (e) hanno sempre offerto servizi ottimali."
David Drewry, Direttore tecnico per AIM Composites"Non abbiamo mai lavorato con Babcock Wanson prima d'ora, ma ho trovato il servizio fornito di altissimo livello."
— Nicola Lord, Responsabile di stabilimento, Blackburn Chemicals"Le apparecchiature Babcock Wanson si sono dimostrate efficienti e affidabili e la loro assistenza è sempre impeccabile".
Keith Netting, Responsabile sviluppo prodotti e industrializzazione, Gurit Composite"I riscaldatori sono ben costruiti, di facile manutenzione e vantano prestazioni ottimali. Una delle unità presenti in loco è rimasta in funzione pressoché 24 ore su 24, 7 giorni su 7, per 360 giorni, facendo rilevare un solo guasto in otto anni. I comandi sono diretti, senza aggiunte complesse o superflue, e sono realizzati in modo da consentire lo svolgimento delle attività necessarie e garantire un corretto funzionamento".
Allan Goulden, Direttore tecnico di Eco-Oil"Il nostro obiettivo principale era ridurre i costi energetici e sapevamo di poter ottenere risparmi notevoli passando dal vapore al fluido termico come fonte di calore per il nostro processo. Abbiamo studiato in dettaglio le opzioni disponibili e questo ci ha portato a ritenere che Babcock Wanson potesse offrire la soluzione migliore. Finora abbiamo avuto ragione: il sistema è facile da usare, con un ottimo controllo e ci ha permesso di ridurre i costi energetici in maniera considerevole."
Douglas Watt, Responsabile di processo Senior, Eastham Refinery Ltd"I riscaldatori hanno soddisfatto completamente le nostre aspettative: sono facili da utilizzare e ci hanno permesso di ridurre in maniera significativa i costi del carburante rispetto ai nostri precedenti riscaldatori a olio."
Peter Shrimpton, Responsabile dei progetti di ingegneria di Bridgnorth Aluminium Ltd"Non avevamo familiarità con i prodotti Babcock Wanson, ma non abbiamo riscontrato alcun problema; basta accendere e funzionano molto semplicemente. Anche l'assistenza ricevuta da Babcock Wanson è stata eccezionale".
You must be logged in to post a comment.