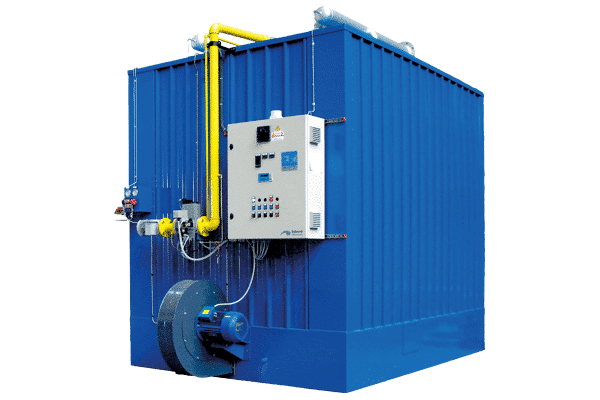
Chris Horsley, Managing Director of Babcock Wanson, looks at the alternative to steam as brewers’ heating method of choice
In the brewery sector steam has traditionally been used as the heating method of choice.
Everyone understands steam. Fire tube boilers and, to a slightly lesser extent, steam generators have been providing brewers with steam based process heating for decades. Wort production is an energy intensive process requiring considerable amounts of heat. These traditional heating methods have performed well and delivered on this time and time again.
So why change now and what’s the alternative?
The alternative is thermal fluid heat systems. As to why change now, I’d suggest that traditionally the major brewers making millions of gallons of beer and lager will continue to use large firetube type steam boilers and steam generators. However, with the incredible upsurge of the craft beer market, made by small, independent brewers, steam should not always be considered to be the most attractive or affordable solution.
In comparison to the major players in the industry, these independent brewers are producing small quantities of beer, to exacting standards. Yet the brewing process is essentially the same. As a result, if steam is chosen as the heat source, a smaller scale version of a steam plant is required, with all the cost, skilled labour and inspection requirements of a major brewer.
Opting for thermal fluid heating removes all of these issues in one go and, more importantly, doesn’t affect the final beer’s flavour. Thermal Fluid systems are far easier to use and therefore require no specialist staff, are very compact and have considerably lower energy consumption.
Thermal fluid heating is based on a similar principle to a domestic hot water system. It consists of a heater connected to carbon steel flow and return pipework which can provide heat to one or more users or systems. Instead of water running through the pipework, a thermal fluid – most often a simple oil – is used as the heat transfer medium.
One of the key factors in achieving very high levels of system energy efficiency is the ability of a thermal fluid system to work at high temperatures (up to 350°C in standard form) in a simple closed loop. When compared to a steam system this means no change of state of the fluid, so no condensate and therefore no flash steam losses, no blow down losses or make up water required, no effluent discharge and completely corrosion free operation without the need for expensive chemical treatment. It all adds up to substantial savings.
The first wort boiler to use a Babcock Wanson thermal fluid heater – and possibly the first thermal fluid heater in the brewing sector to the best of our knowledge – was Wye Valley Brewery in Herefordshire. At the Wye Valley 80brl plant, the external wort boiler system and copper are located adjacent to a Babcock Wanson TPC1000B Thermal Fluid Heater, which is LPG fired. The thermal fluid circulates through the wort boiler heat exchanger which, due to the use of thermal fluid, does not require rating as a pressure vessel. Once boiling, the wort will thermosyphon through the heat exchanger without the need to use the copper casting pump at all.
The wort boiler control system was a major consideration to Wye Valley. Their biggest seller is Herefordshire Pale Ale which has a colour of only 8 EBC, so great care is required with colour pick up. The integrated control system, coupled to a fixed flow of thermal fluid and the Babcock Wanson burner control system, has ensured very precise heat transfer to the process which also means reduced overall fuel costs.
More recently, Freedom Brewery – the UK’s original craft lager brewer – has swapped to using a Babcock Wanson TPC400B Thermal Fluid Heater at its Abbots Bromley site in Staffordshire, in a similar set up. Commenting on their decision to move away from steam, Andrew Taylor, Director at Freedom Brewery, says: “we chose thermal fluid because it was more cost-effective to install and run, has a smaller space requirement than steam and provides a greener solution.” Certainly thermal fluid heating systems are highly compact and require no specialist site work meaning they can be sited in a convenient location close to the user, without needing specialist plant rooms or long runs of distribution pipe work.
Since being installed, Andrew is extremely pleased with the thermal fluid heater’s performance: “the heater has performed in excess of expectations. It is compact, much faster to bring into operation than a steam boiler and, because it does not use steam as the heat transfer medium, is much cheaper to operate as there is no water treatment and no condensate return.”
But for Andrew ultimately the reduction in energy costs have really been the most outstanding factor: “Our energy costs per litre brewed are now a sixth than they were before!” That’s partly because the system precisely matches fuel input to plant energy requirements for highest practicable operating efficiency. With lower energy input demand also comes lower total exhaust emissions – another environmental benefit for Freedom Brewery.
Using thermal fluid as opposed to water has other key benefits including removing the problems caused by scaling if water treatment malfunctions or freezing due to low ambient temperatures, as well as improved safety.
Whilst thermal fluid heaters are used extensively across a wide range of industries, they remain little known in the brewery sector. This is strange as their benefits often outweigh those of steam considerably, especially when it comes to energy consumption, as I hope I have demonstrated here. The continued reliance on steam I believe comes down to tradition; all good and well, but just because it’s always been done this way doesn’t mean there isn’t a better, alternative solution: thermal fluid heat systems.
Babcock Wanson offers a complete range of products and services for boiler houses and other process heating needs. These include steam boilers, thermal fluid heaters, rapid steam generators and hot water boilers to VOC and odour treatment by thermal oxidation, water treatment or process air heating solutions. For more information, please contact Babcock Wanson on 020 89537111 or info@babcock-wanson.co.uk
You must be logged in to post a comment.