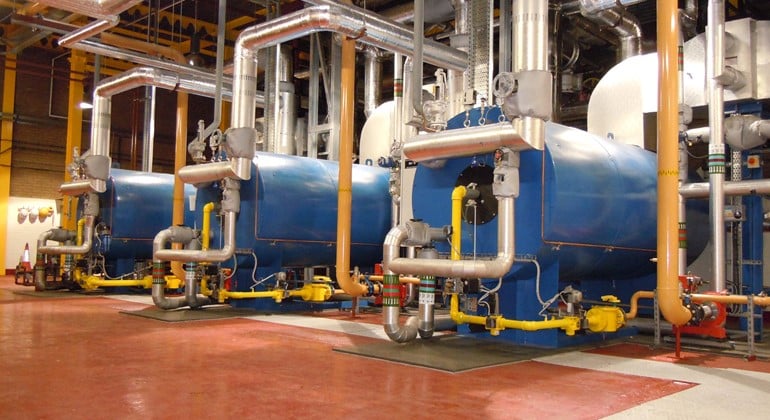
One of the key developments in the heat raising field that has led to dramatically reduced bills is the development of high efficiency thermal fluid heating systems, the best of which will include integral economisers to ensure very low fuel consumption even when operating at high fluid temperatures. Thermal fluid heating systems can use 20-50% less energy to transfer the same amount of heat when compared to traditional steam heating systems.
To achieve high levels of system energy efficiency a thermal fluid system works at high temperatures (up to 350°C in standard form) in a simple closed loop, without change of state of the fluid leading to no condensation and therefore no flash steam losses. There is also no make up water required, no effluent discharge, and a corrosion free system without the need for expensive chemical treatment. It all adds up to substantial savings.
A thermal fluid heating system is compact and needs no specialist site work meaning it can be sited in a convenient location close to the user, without needing specialist plant rooms and distribution pipe work.
Webster & Horsfall converted from steam generators to a Babcock Wanson TPC600B thermal fluid heating system in 2011 for manufacturing high-strength drawn wire. This was undertaken as part of a project in conjunction with the Carbon Trust to reduce costs and carbon footprint and improve efficiency through modernising machinery and infrastructure. As a result, they saw a 35% drop in annual kW usage , proving to be one third more efficient, easier to maintain and quicker to respond than the previous steam based system.
This tale of energy savings is often repeated by companies investing in modern heat raising systems.
TRB is a leading Original Equipment Manufacturer that manufactures tailor-made lightweight solutions and bespoke fabricated assemblies. The company upgraded from steam heated platen presses to a gas fired Babcock Wanson TPC600B thermal fluid heating and cooling system, whilst at the same time installing new platens. They reported having received 70% cost saving, not having to deal with corrosion, and reduced emissions. It resulted in an increased production capacity with better quality products, giving TRB a competitive edge.
For TRB, energy savings are important, but just as crucial is the ability to maintain constant temperature control. With a thermal fluid heating and cooling system, temperature control is far more accurate without getting temperature drop off. The system also provides programmable ramp up temperatures and a controlled cool down over a set time.
But it is important to note that thermal fluid heating systems do not suit every industry’s requirement as they are incapable of providing both direct and indirect heat required simultaneously for some processes. For those, the new breed of high efficiency steam generators, such as Babcock Wanson ESM steam generators, that consume less energy and have reduced emissions along with improved safety and simplicity of control are the answer. They give operating efficiencies of up to 96% with very low overall emissions.
Modern Steam Generators include an accurately controlled burner which creates a defined heat input to a double coil of steel tube through which a precise quantity of feed water is pumped. A steam / water separator is incorporated at the coil outlet to ensure good conditions for steam production within the coil itself and good quality dry steam at the separator outlet.
Bedford Hospital switched to modern Steam Generators and reported carbon savings of 1687 tonnes of CO2e and cost avoidance on boiler fuel alone of circa £525,000. They installed three Babcock Wanson 2500kg/h ESM Steam Generators fitted with high efficiency exhaust gas economisers. The primary fuel used is gas (with one unit configured for duel fuel operation as a precautionary measure), which is cheaper, has resulted in on-site fuel storage largely being eradicated, and a quieter, cleaner and cooler operation.
Much like these businesses, large and small business can shift to thermal fluid systems or modern Steam Generators and make impressive savings – it all simply boils down to making the right investment.
You must be logged in to post a comment.