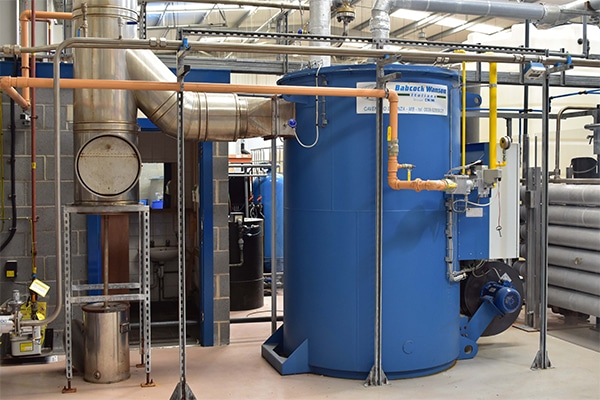
Promethean Particles has built the world’s largest continuous multi-material nanoparticle manufacturing plant, based in Nottingham, producing in excess of 1000 tons per year. Its unique reactor design allows for continuous (as opposed to batch) production and flexibility, enabling it to produce a huge variety of materials to customer’s specifications. The flexibility is largely down to the wide temperature range achievable with its process, which is important as there is a correlation between the temperature and particle size.
Babcock Wanson was one of a handful of manufacturers approached by Promethean Particles, and the only one to provide a suitable solution. The heater is based on a Babcock Wanson TPC 1000B, but with very special inners and controls. For this bespoke heater Babcock Wanson designed and manufactured a specially wound continuous coil assembly to form the main heating surface using ASI 321 9mm thick stainless steel, as opposed to the usual 4mm carbon steel for a standard industrial type water heater. The core of the tube is very small. This material and thickness were chosen to meet the pressure and temperature demands of the process to be able to produce supercritical water at up to 250 bar and 450°C.
Several challenges were faced along the way, including designing the heater with the ability to accept variations in water flow (between 600-3000 kg/h per hour) and heat input within quite wide parameters; developing specialist welding techniques to cope with the material to the design pressure required and specifying and installing specialist instruments and controls to work at these temperatures and pressures.
All in all it took seven months to design and build. The combustion system, control scheme and software were designed in-house by Babcock Wanson. Relevant mountings, safety valves, pressure controllers and differential controllers were sourced and fitted in house to enable PED approval. A hazard and operability study (HAZOP) were carried out between Babcock Wanson and Promethean engineers to review the controls and integration with the site control Scada system.
The resulting heater is now an integral part of the process, which includes return fluid heat recovery to limit the final temperature rise of the fluid to 90°C. This brings it up to 360°C water at 270 bar to take it to the temperature required for the supercritical condition. With standard water, this would typically require just 314kW, but as the supercritical water is so dense up to 1000kW is needed.
The supercritical water is then pumped into the reactor at the same time as the precursor where it mixes and forms the product. The product leaves the reactor through a specially constructed section at 350°C. It then goes through the heat exchanger to cool it down and recover waste heat and the pressure is reduced before passing the product into a holding tank. Depending on the product, further processing may then be required.
The entire process is controlled by sophisticated software and is encased in toughened casing for safety.
Lewis Neve, Production Engineer at Promethean Particles, comments: “The heater is running as expected. Babcock Wanson knew what they were doing and it went very smoothly. They have also been very easy to work with, very professional in the way they communicated with us and the fact that they were in constant communication made it easier for us.”
Babcock Wanson offers a complete range of products and services for boiler houses and other process heating needs, from steam boilers, thermal fluid heaters, rapid steam generators and hot water boilers to VOC and odour treatment by thermal oxidation, water treatment or process air heating solutions. The company aims to help optimise customer’s energy production with high quality products and efficient service.
For more information, please contact Babcock Wanson on 020 8953 7111 or info@babcock-wanson.co.uk or go to www.babcock-wanson.co.uk