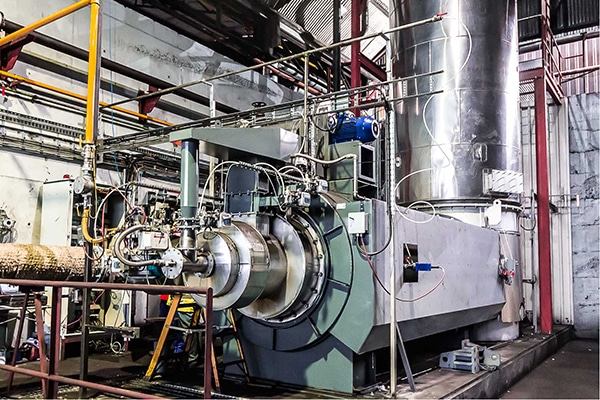
Arigna Fuels in County Roscommon in Ireland is an innovative company that converts biomass into a high energy, high density and greener fuel with the same burning characteristics as many existing fossil based fuels. It developed its own pioneering processing system based around torrefaction (the process of heating biomass in the absence of oxygen) to achieve this.
At the heart of Arigna’s system are two reduced atmosphere reactors. One is used to dry the biomass and the other for the torrefaction process itself. The initial reactor heats the raw biomass to remove the water content and dry the material. This also kick-starts a thermal reaction to break down the hemicellulose within the plant structure. The dried biomass material is then fed through to the second reactor where torrefaction takes place at a higher temperature. Both reactors are heated using thermal fluid.
As you might expect, such a process requires considerable energy input; something Arigna was keen to minimise to produce a truly sustainable product. A clever solution was developed in conjunction with Babcock Wanson based around the integration of a Recuperative Thermal Oxidiser fired on the gas produced from the torrefaction process with heat recovery to thermal fluid. This system means the process is mostly self-fuelling and also helps Arigna meet the site emission targets.
Relatively low calorific syngas is discharged from Arigna’s reactors. The Babcock Wanson Recuperative Thermal Oxidiser oxidises that gas at 850⁰C for approximately 0.8 seconds before it is discharged into the atmosphere as a harmless exhaust. Recuperative Thermal Oxidiser are ideal for industrial processes where there is a combination of high process energy demand and effluent oxidation. They are becoming increasingly popular due to their quick start up and high energy recovery, plus they are safe and reliable to operate.
At the same time the gas is being oxidised, the heat recovery unit that forms part of the Oxidiser system recovers up to 2.5MW of energy to thermal fluid from the gas exhaust stream. The heat recovery device is based on a vertical, first gas-pass upwards design of coil type assembly with gas reversal into a plenum between the coils.
Heat recovery from the Oxidiser is linked into the site thermal fluid system which uses a TPC1500B Babcock Wanson Thermal Fluid Heater. This enables the process to be started quickly and efficiently whilst the Oxidiser and reactors warm up. A propane fired burner on the Oxidiser is used during start-up, but is quickly reduced to a small back up flame of 50-100kW as the process gas takes over the fuelling demand as part of this clever self-fuelling process.
The entire oxidisation and heat recovery process is PLC controlled, with HMI operator interface, plus Ethernet connection to Arigna’s site SCADA system.
TPC Thermal Fluid Heaters are ideally suited to this process due to their environment credentials, having an integral burner which ensures efficient use of fuel, plus low overall emissions. Furthermore, their design, featuring an integral air-cooled outer case that acts as both a combustion air pre-heater/economiser and as a constant barrier between the hot combustion gasses and the outer structure, ensures stress free operation for long equipment life.
At the end of the process, the product is cooled and briquetted for a greener, more sustainable fuel.
“As the process was developed and commercialised, operating parameters had to be adjusted and altered numerous times. The recuperative thermal oxidiser proved to be very resilient to the parameter changes and was easily able to meet site emission targets over a wide range of operating conditions with heat recovery efficiency exceeding expectations over an extended operating range.” commented Peter Layden, R&D Director, Arigna Fuels. “We are in detailed design stage for a much larger plant and intend to use this technology in the next stage of our development of replacements for our existing fossil fuel products.”