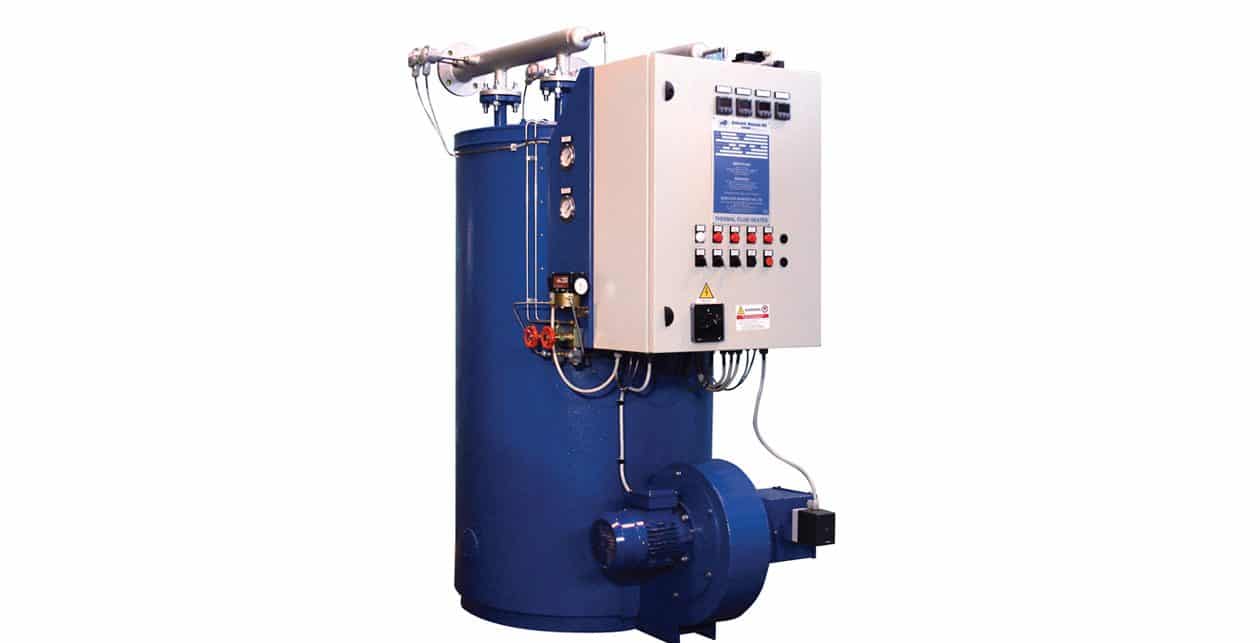
A Babcock Wanson TPC 200B Thermal Fluid Heater has been installed at Bridgnorth Aluminium Ltd as a key component in its exhaust air purification system.
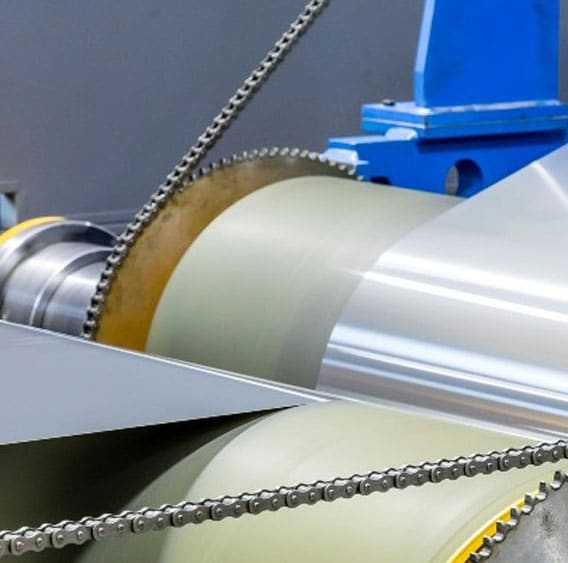
TPC 200B Thermal Fluid Heater
Bridgnorth Aluminium Ltd is the UK’s only manufacturer of lithographic aluminium strip with a purpose built, state of the art rolling mill and stretch levelling line in its Shropshire site. The company is focussed on maintaining a clean alloy system with its high purity aluminium alloy product range, which requires considerable technical knowledge of the process requirements.
As part of a planned expansion, Bridgnorth Aluminium Ltd recently purchased a refurbished rolling mill from overseas. As with all rolling mills that use oil as a coolant and lubricant, amounts of oil are emitted in their exhaust. In line with best practice, Bridgnorth Aluminium Ltd has installed an Achenbach AIRPURE® exhaust air purification system to separate and recover hydrocarbons from the mill exhaust – in this case tetracene. Babcock Wanson’s TPC 200B Thermal Fluid system forms an integral part of this process, heating the exhaust air to enable the AIRPURE® system to recover virtually all rolling oil. Babcock Wanson not only supplied the new TPC 200B thermal fluid system, but was also involved in laying out the pipework and connections to the heat exchangers.The Result
The TPC 200B is a fully automatic coil type, multi-pass thermal fluid heater complete with integrated burner, control system and safety devices. It provides optimal distribution of the heat, high fluid velocity in the exchange tubes and continuous flow monitoring to ensure long thermal fluid and system life and the highest level of safety.
TPeter Shrimpton, Engineering Projects Manager at Bridgnorth Aluminium Ltd, comments on the TPC 200B Thermal Fluid Heater: “the original manufacturers of the rolling mill equipment recommended that we use a thermal fluid system as part of the exhaust air purification system. We hadn’t used this before and were unfamiliar with Babcock Wanson, but we’ve had no problems with it whatsoever; you simply switch it on and it works – simple as that! The service we have received from Babcock Wanson has also been great.”
TWhilst Bridgnorth Aluminium Ltd hasn’t been using the system long enough to gather comprehensive energy efficiency data, it is expecting considerable energy savings. Babcock Wanson claim between 20-50% energy savings can be made by using a TPC B thermal fluid heating system, when compared to the transfer of the same amount of heat using traditional steam boilers. These savings are achieved as the thermal fluid does not need to change state to transfer the heat, as would be the case with steam, which means no trap losses, no blowdown losses and no flash steam losses. This also makes for much simpler operation and very low maintenance needs. With lower energy input demand also come lower total exhaust emissions so thermal fluid systems are much kinder to the environment.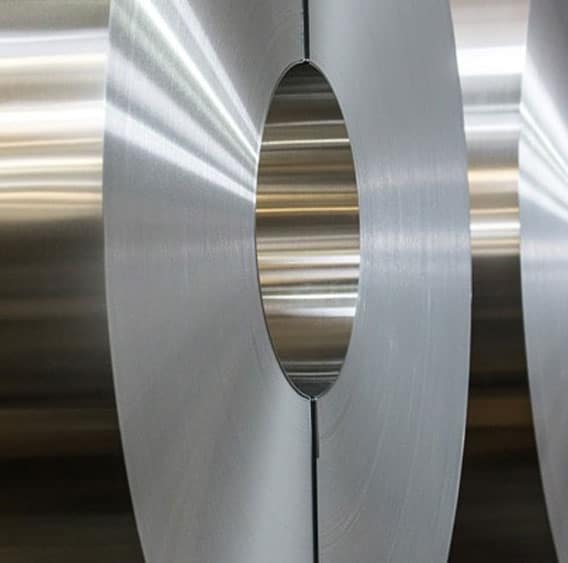
Customer Testimonials
— Loucas Antoniou, Engineering Manager at Bakkavor Meals London“The Thermal Oxidiser is the most efficient way of removing any smells and it’s also very straightforward to use. We have been a customer of Babcock Wanson for many years and have always enjoyed a good service.”
— Carbon Trust Annual Report 2009/10“A major carbon footprint reduction will be achieved when the scheme currently in progress to change the main boiler fuel from heating oil to gas is completed in summer 2010. This £900k project will reduce our carbon emissions via energy usage by around 15% by removing the need to use heavy fuel oil, as the new boiler plant will use natural gas as its main fuel source.”
— Webster & Horsfall“What we hadn’t expected initially though is the level of control the new system provides us with; it’s amazing. It alerts us to any potential issues, is easy to maintain (no annual statutory inspection is required) and is quick to respond. All that and it doesn’t take up much room.”
— Peter Connolly, Production Engineer at Vacu-Lug“The ESM 2000 installation, together with an ongoing programme of process plant lagging and steam trap maintenance, has enabled us to significantly reduce our gas usage and cushion the company against rising gas prices.”
— Dave Scrivens, Facilities Manager at Plastic Omnium“Babcock Wanson’s expertise and ability to provide a whole package made them the leading contender for this project. On further investigation, their proposal was also commercially viable, which sealed the deal.”
— Denis Kelly, Engineering & Construction Manager at Stolthaven Dagenham“The Thermal Fluid Heaters themselves were ideal for this project as they are based on mature technology and are well proven in the field. They are robust and also require very little maintenance.”
— Ian McQuarrie, Engineering Manager at Puredrive“During my three years here, the Steam Generators and Thermal Fluid Heaters have worked flawlessly. Babcock Wanson carries a good name in the business for both quality and equipment longevity. Their knowledge, company wide, is exceptional and the whole package from installation through to service is managed professionally.”
— Jason Hall, J&A Young Engineering Manager“We had estimated our steam requirements, but Babcock Wanson had the experience to understand that we had underestimated this. In fact, the erratic nature of the steam loads would have been impossible to meet under our existing spec. Babcock Wanson was able to identify this as well as provide a very energy efficient solution with a number of enhanced features”.
— Lee Bullen, Corrugated Services Manager at Board24“It’s running very well, both easy to use and efficient. The service from Babcock Wanson has also been very good.”
— Peter Shrimpton, Engineering Projects Manager at Bridgnorth Aluminium Ltd“We were unfamiliar with Babcock Wanson, but we’ve had no problems with it whatsoever; you simply switch it on and it works – simple as that! The service we have received from Babcock Wanson has also been great.”