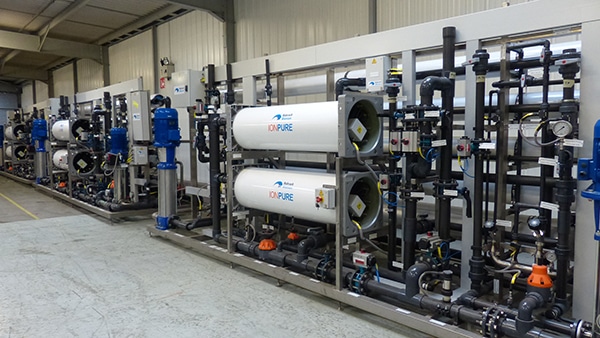
Feeding boilers intended for the production of steam for the requirements of the energy recovery centres for waste
For the requirements of the energy recovery centres for waste, Babcock Wanson is developing a solution for the production of highly demineralised water to feed steam turbines via high pressure boilers.
Ideally, Babcock Wanson is involved from the project preparation phase, drawing on its extensive experience in the challenging field of energy and the environment to provide the most suitable solution in accordance with the requirements and specifications of the end customer and the applicable standards.
The steam turbines used to generate electricity, or heat, require the highest quality steam, as dry and pure as possible.
To achieve this, it is essential to supply the boilers with ultra pure water, free from all mineral and organic impurities that could affect the quality of the steam to be supplied.
This ultra pure water must meet the VGB-10 standard p14/111 and those of the equipment manufacturers with a conductivity of < 0.15µS/cm, a silica content of < 20ppb and a sodium residual of < 10ppb.
The solution provided by Babcock Wanson offers highly demineralised water with an overall water efficiency approaching 90%.
Babcock Wanson’s expertise in the field of water treatment is fully utilised to attain this result.
The solution: A unit consisting of two demineralisation treatment stages connected in series:
A first stage of primary demineralisation by reverse osmosis (RO) removes more than 99% of contaminants from the raw water, and a second stage of finishing by electrodeionization (EDI) ensures that the quality requirements of ultra pure water are met.
To ensure the reliability of the demineralisation process, the mains water supply used to feed the demineralisation station must first be pre-treated using various equipment adapted to its physical and chemical characteristics:
Pre-treatment
To prevent particle deposits on the reverse osmosis membranes, the following is implemented:
Pre-filtration of raw water
A pre-filtration station with a 50µm safety bag is installed because mains water can contain solid particles.
Cartridge filtration
Upstream of the microfiltration is a cartridge filtration station, with a filtration threshold of 5µm, allowing larger particles to be retained “relieving” the final microfiltration station by reducing the replacement frequency of the 1µm filter cartridges.
Microfiltration
To avoid problems of membrane fouling by solid particles (lowering of the fouling index), the osmosis unit is equipped with a microfiltration station using cartridges with a filtration threshold of 1µm.
To prevent mineral deposits on the reverse osmosis membranes, the following is implemented:
Softening on Resins
A duplex or triplex resin softening station: it consists of a set of two or three units operating alternately, two devices in simultaneous production, the third in regeneration and waiting for changeover.
The softeners are regenerated by a salt pellet brine, stored and diluted in a tank before each regeneration.
To prevent the oxidising effect of chlorine on reverse osmosis membranes, the following is implemented:
Dechlorination
The mains water to be treated has high levels of chlorine. Since the presence of oxidant is not compatible with the long-term use of reverse osmosis membranes, a regulated dosing unit for chlorine reduction products is installed to prevent the problem.
In order to limit the CO2 level (not retained by reverse osmosis) and in anticipation of an optimum finish on the EDI, pH adjustment is carried out
Alkalinization
A diluted soda solution is injected in a regulated manner into the high pressure pump inlet.
Once the mains water has been pre-treated by this process, it can then be directed to the two demineralisation stages:
1st demineralisation stage: Primary Demineralisation by Reverse Osmosis
The primary demineralisation station consists of several osmosis units connected in parallel and producing demineralised, degassed water with a conductivity of less than 10µS/cm.
The pre-treated raw water is supplied to the inlet of a high pressure pump which pressurises the water to be treated so that the reverse osmosis effect can be activated. After passing through the membranes, the permeate is collected at the pressure tube outlet and monitored by conductivity meter.
Part of the concentrate is recycled at the top of the osmosis unit to maintain a sweep rate across the membranes, the second fraction of concentrate is recycled after further treatment (concentrator, see below).
The different flow rates of permeate, recycled concentrate and discharge are adjustable and controllable by flow transmitters. This equipment allows the adjustment and verification of the osmosis unit conversion rate.
Each time the unit is shut down, automatic rinsing (flushing) is carried out to evacuate the concentrate in the modules avoiding any deposit of salts within the membranes
2nd demineralisation stage: Finishing Demineralisation by Electrodeionization
The demineralised water polishing station consists of several electrodeionization units. Electrodeionization is achieved through modules using ion exchange resins that are continuously regenerated by water electrolysis, without the use of chemical reagents.
Several identical lines, each operating at a specific flow rate, produce water with a conductivity of less than 0.15µS/cm in most instances.
After passing through the EDI unit, the water is collected at the outlet of the modules and checked by a conductivity meter and silica meter before being stored in a tank.
Finally, a series of concentrators completes the treatment process:
All of the continuous discharge, where the salts in the feed water are concentrated, is returned to a raw water tank, via pre-treatment using concentrators. Concentrates from primary osmosis units and EDI modules are collected in buffer tanks for reprocessing in several osmosis concentrators. The permeate produced is recycled at the top of the unit and the concentrate is the only water discharge from the overall purification process.
Water balance of the treatment plant:
The primary reverse osmosis (RO) demineralisation station operates with an internal conversion rate (ratio between produced water flow and supply water flow) of around 75%.
The electrodeionization station (EDI) allows demineralised water to be “polished” with an internal conversion rate of over 90%.
To limit the overall discharge from the demineralisation station and improve its performance, the discharge or concentrates from the primary osmosis units and electrodeionization modules are therefore re-treated in osmosis concentrators, and the water produced is reintroduced into the raw water tank, upstream of the softening/pre-treatment station.
To meet the necessary consumption rates and availability requirements, enhanced redundancy is ensured with several identical water treatment lines connected in parallel.
In addition to the demineralisation station, Babcock Wanson also provides auxiliary and complementary solutions and equipment for projects of this type, such as low-pressure boilers, chemical treatment stations for the LP and HP networks, low-pressure thermal degassers, as well as chemical dosing for the neutralisation of the site’s liquid waste.
The water softening station can also be used to supply emergency low pressure boilers, which are always available to supply process LP steam to external industrial users. Therefore the site increases its profitability by operating as a process steam supplier to external customers.
The solution implemented by Babcock Wanson allows for highly reliable water production, with a unit availability rate close to 100%. It facilitates the water efficiency optimisation of the treatment plant and the factory and limits the use of chemical reagents.
Babcock Wanson is able to apply its entire spectrum of expertise in the field of water treatment, from design and engineering, to production, final testing and activation, as well as training of operating personnel, to provide the most efficient overall solution tailored to the customer’s requirements.
These projects are carried out by the water treatment department, supported by a design office and project managers as well as a local network of water treatment technicians for the implementation of the project.
You must be logged in to post a comment.