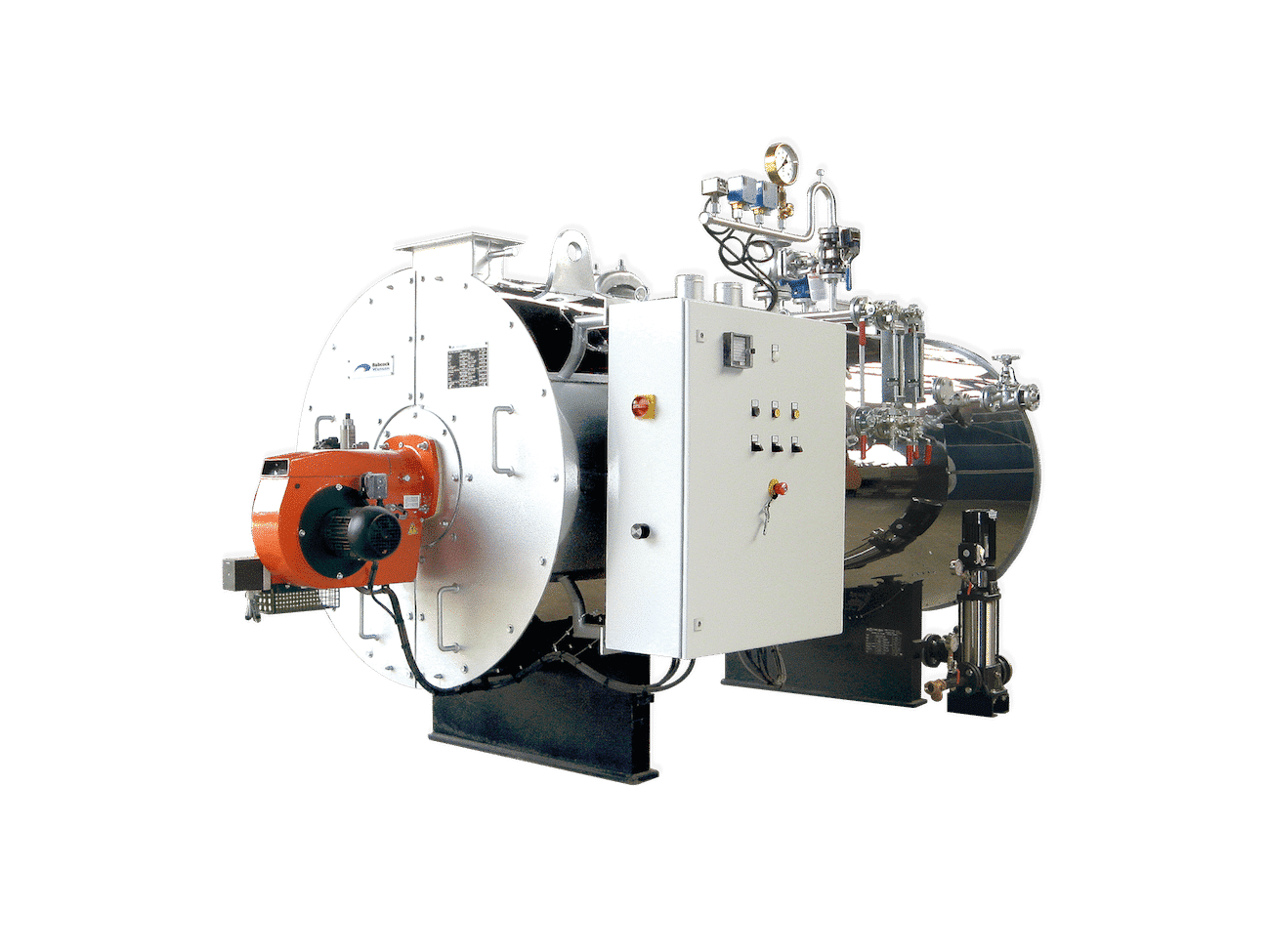
Over the past quarter of a century industry has slowly but steadily moved away from steam generation technology as the most popular industrial process heating method. Sometimes the move has been to direct gas firing but on many occasions indirect heating of a process is still considered the best solution and for these applications the use of thermal fluid heating has proven to be the most highly energy efficient solution.
So is the end inevitable for steam generators?
In one word: No. I believe steam for process use, especially in the food industry, has a long term future as there are a great many key applications – most notably where both direct and indirect heating are required simultaneously – where it simply can’t be matched.
Before we go any further, I should point out that Babcock Wanson manufactures both thermal fluid heating systems and steam generators so my argument in favour of steam for certain applications is not based on our product inventory, but on our years of experience in process heating.
Steam generators operate on the same principle as other steam raising technology in that water is confined in a restricted space and is heated by burning a fuel source, such as gas or oil. The heat is transferred through the walls of the tubes thereby heating the water and ultimately creating steam.
A thermal fluid heating system consists of a heater connected to flow and return pipe work which can provide heat to one or more users or systems. Instead of water running through the pipework, a thermal fluid is used as the heat transfer medium.
Much of the appeal of thermal fluid heating systems has been based on their efficiency, compact size, ease of operation. Steam generators, on the other hand, need pre-treatment and conditioning equipment to prepare the water and to protect the steam raising equipment from scale and corrosion, which can be expensive. A steam system will also need more associated equipment than thermal fluid heaters, adding to the cost and taking up more space. Steam systems are also generally uneconomic when the process temperature is over 200°C. Lastly but perhaps most importantly, a steam system will rarely operate as a fully closed loop so will suffer higher general heat losses due to the change of phase (condensate to steam and back to condensate). These are all real life operating costs which should not be overlooked when deciding on the best solution for a particular heating requirement.
However, when comparing the two different systems, it’s important not to base your considerations on the traditional steam raising boilers. Modern coil type steam generators really are a different kettle of fish. A precisely controlled burner creates an accurately defined heat input to a double coil of steel tube through which a precise quantity of feed water is pumped. Only a small amount of excess water is fed into the coil. A steam / water separator is incorporated at the coil outlet to ensure good conditions for steam production within the coil itself (while avoiding superheat) and good quality dry steam at the separator outlet.
Using this method steam generators maximise efficiency, reducing overall carbon emissions. Babcock Wanson ESM steam generators, for example, give operating efficiencies of up to 96% with very low overall emissions.
Compared to older steam generating technology, coil type steam generators can not only be considerably more energy efficient and environmentally friendly, but they can be safer to operate as the chance of a pressurised water explosion is virtually eliminated. They tend to be smaller in overall footprint, easier to control and quieter and cleaner in operation. They are also very quick in raising steam (as quickly as five minutes from a cold start to full output); a very important feature when the process demand is intermittent or starts and stops on a daily basis.
So steam generators have come a long way from their predecessors.
Where steam generators really come into their own though is with their ability to transfer heat at a constant temperature and with high heat transfer rates due to the latent heat given up during condensation.
It’s this stable and efficient heat transfer at lower temperatures that makes steam generators ideal for heating large quantities of process hot water.
I believe one of the reasons for the demise in steam equipment sales is not necessarily that industry doesn’t want steam; it’s actually because of the scarcity of steam generator manufacturers. It takes exceptional expertise to design and manufacture steam generators and more importantly to provide the engineering support and staff necessary for a successful installation and many manufacturers have simply opted out.
Babcock Wanson offers a complete range of products and services for boiler houses and other process heating needs. For more information, please contact Babcock Wanson on 020 89537111 or info@babcock-wanson.co.uk.
You must be logged in to post a comment.