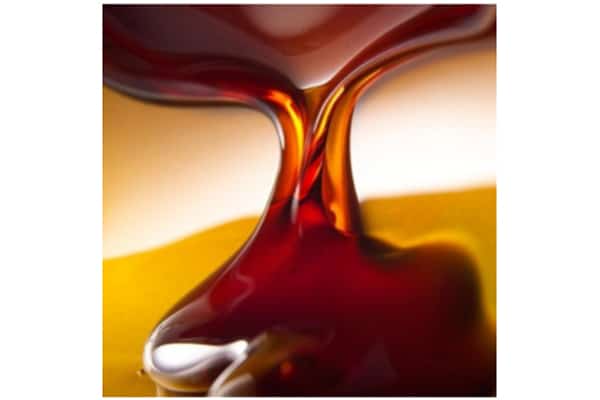
The NIGAY family company, based in FEURS (42-France), specialises in the manufacture of caramels for use in various forms by craftsmen and food processing industries (annual production of 68,000 tons).
Driven by its dynamic growth and committed to an ISO 50001 approach, it has decided to convert its steam production equipment from heavy fuel oil to natural gas firing thereby improving both energy utilisation and performance.
It has placed its trust in Babcock Wanson to install a new boiler room, which includes a BWD 80 steam boiler equipped with a Babcock Wanson Modulo+ micro-modulating burner and an economizer. This equipment allows the boiler to operate at very low power with a modulation range from 1 to 12, while maintaining flexibility of use, highest practicable efficiency and a very high response rate.
The economizer recovers part of the heat from the flue gases to preheat the boiler feed water. The boiler room is controlled by a dedicated PLC, making it easy to monitor its performance and operation.
The efficiency of the installation with this level of equipment is circa 95.6% based on the net calorific value of the fuel.. NOx emissions are of the order of 80 mg/Nm, a value well below that imposed by the site operating permit (150 mg/Nm).
The conversion of the boiler room to natural gas has enabled the company to reduce its CO emissions by nearly 30%.
Driven by its dynamic growth and committed to an ISO 50001 approach, it has decided to convert its steam production equipment from heavy fuel oil to natural gas firing thereby improving both energy utilisation and performance.
It has placed its trust in Babcock Wanson to install a new boiler room, which includes a BWD 80 steam boiler equipped with a Babcock Wanson Modulo+ micro-modulating burner and an economizer. This equipment allows the boiler to operate at very low power with a modulation range from 1 to 12, while maintaining flexibility of use, highest practicable efficiency and a very high response rate.
The economizer recovers part of the heat from the flue gases to preheat the boiler feed water. The boiler room is controlled by a dedicated PLC, making it easy to monitor its performance and operation.
The efficiency of the installation with this level of equipment is circa 95.6% based on the net calorific value of the fuel.. NOx emissions are of the order of 80 mg/Nm, a value well below that imposed by the site operating permit (150 mg/Nm).
The conversion of the boiler room to natural gas has enabled the company to reduce its CO emissions by nearly 30%.
You must be logged in to post a comment.