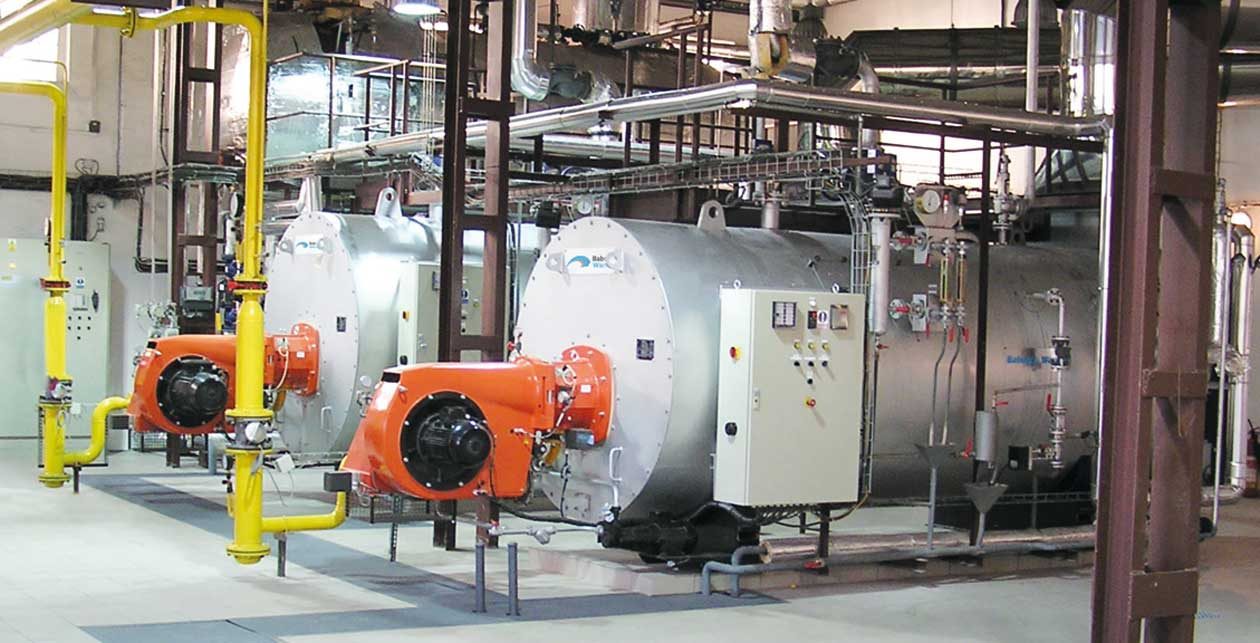
Babcock Wanson Boiler Control Reduces Costs And Meets Yeast Manufacturer’s Complex Steam Demand
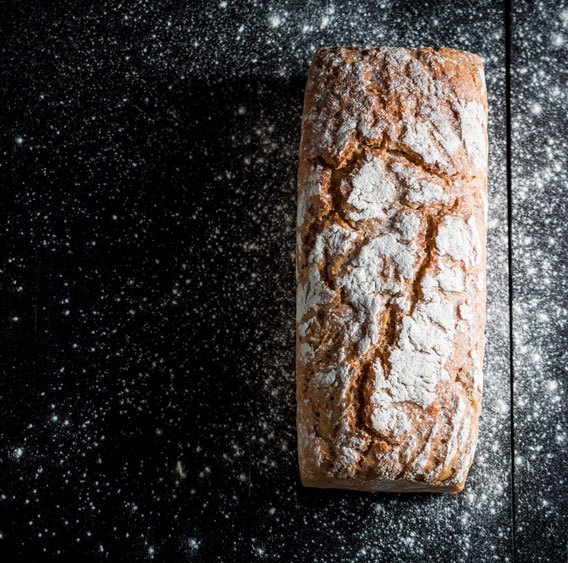
BWD Fire Tube Boilers with Integral Economiser
Yeast production company Lallemand GB has installed two Babcock Wanson BWD fire tube boilers with integral economiser and BW72H control system into its Felixstowe plant – the UK’s largest fresh yeast production facility for the UK baking industry.
The BWD60 boilers replace the existing three-pass fire tube boilers in the main plant room that had been installed in 1967 and had come to the end of their working lives.
Babcock Wanson was an obvious choice for Lallemand not only because of its reputation in the industry, but also because Lallemand already use Babcock Wanson boilers across other sites and have very been satisfied with their performance. Evert Wijnberg, Project Manager at Lallemand GB, has been pleased with the level of service provided: “Babcock’s performance has been good throughout the whole process. We were able to do as we said that we would do. What is also worthwhile mentioning is that Babcock is prepared to evaluate their performance with the customer and wants to improve by doing so.”
A System to Suit a Complex Need
Choice of boiler type, as Evert explains, was more complex as it required a degree of flexibility: “In selecting the size it helped a lot that we have a good understanding of our demand pattern. On the other hand we have had a lot of “fuzzy logic” as we expect quite some expansion on our site, but it is not yet fully clear what it will be.” The results have been positive: “What has come out are BWD60s have a slightly higher capacity than the boilers they replace.
The other key element to the boiler configuration was the use of Babcock Wanson’s prestige BW72H control system which greatly alleviates the normal demands of running a steam boiler with its in built self checking controls and minimal testing needs. This has enabled the company to both manage its complex steam demand pattern while helping to reduce costs. Evert explains: “Unfortunately we have considerable load swings which are the consequence of the way we sterilize equipment. This is a situation that we can manage best when we can deploy intelligent algorithms. The control system of the boilers provides the platform for doing this.
“The more successful we are at managing the balance between the two boilers and the steam demand pattern, the more we can reduce the energy bill and make the best return in our investments..”
The BW72H control system has also allowed for reduced operator control as it continuously, automatically monitors the environment, thus reducing costs further while improving efficiency.
Further expansion at the Felixstowe site is imminent and Lallemand GB are considering the use of Babcock Wanson Thermal Fluid units to provide the required high operating temperatures needed as part of this development.
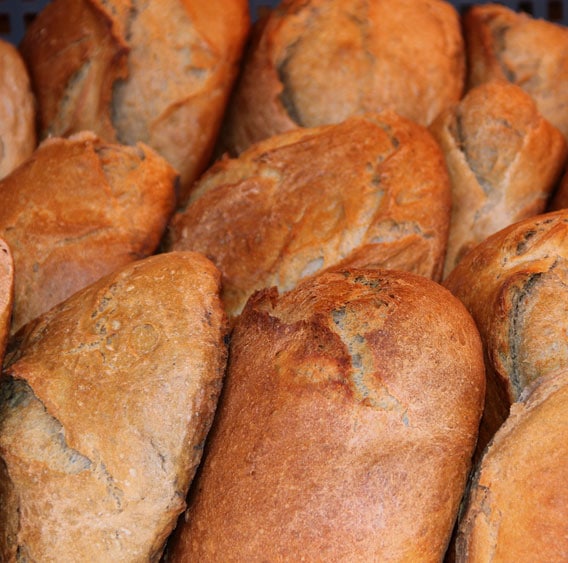
Customer Testimonials
— Loucas Antoniou, Engineering Manager at Bakkavor Meals London“The Thermal Oxidiser is the most efficient way of removing any smells and it’s also very straightforward to use. We have been a customer of Babcock Wanson for many years and have always enjoyed a good service.”
— Carbon Trust Annual Report 2009/10“A major carbon footprint reduction will be achieved when the scheme currently in progress to change the main boiler fuel from heating oil to gas is completed in summer 2010. This £900k project will reduce our carbon emissions via energy usage by around 15% by removing the need to use heavy fuel oil, as the new boiler plant will use natural gas as its main fuel source.”
— Webster & Horsfall“What we hadn’t expected initially though is the level of control the new system provides us with; it’s amazing. It alerts us to any potential issues, is easy to maintain (no annual statutory inspection is required) and is quick to respond. All that and it doesn’t take up much room.”
— Peter Connolly, Production Engineer at Vacu-Lug“The ESM 2000 installation, together with an ongoing programme of process plant lagging and steam trap maintenance, has enabled us to significantly reduce our gas usage and cushion the company against rising gas prices.”
— Dave Scrivens, Facilities Manager at Plastic Omnium“Babcock Wanson’s expertise and ability to provide a whole package made them the leading contender for this project. On further investigation, their proposal was also commercially viable, which sealed the deal.”
— Denis Kelly, Engineering & Construction Manager at Stolthaven Dagenham“The Thermal Fluid Heaters themselves were ideal for this project as they are based on mature technology and are well proven in the field. They are robust and also require very little maintenance.”
— Ian McQuarrie, Engineering Manager at Puredrive“During my three years here, the Steam Generators and Thermal Fluid Heaters have worked flawlessly. Babcock Wanson carries a good name in the business for both quality and equipment longevity. Their knowledge, company wide, is exceptional and the whole package from installation through to service is managed professionally.”
— Jason Hall, J&A Young Engineering Manager“We had estimated our steam requirements, but Babcock Wanson had the experience to understand that we had underestimated this. In fact, the erratic nature of the steam loads would have been impossible to meet under our existing spec. Babcock Wanson was able to identify this as well as provide a very energy efficient solution with a number of enhanced features”.
— Lee Bullen, Corrugated Services Manager at Board24“It’s running very well, both easy to use and efficient. The service from Babcock Wanson has also been very good.”
— Peter Shrimpton, Engineering Projects Manager at Bridgnorth Aluminium Ltd"We were unfamiliar with Babcock Wanson, but we’ve had no problems with it whatsoever; you simply switch it on and it works – simple as that! The service we have received from Babcock Wanson has also been great.”
You must be logged in to post a comment.