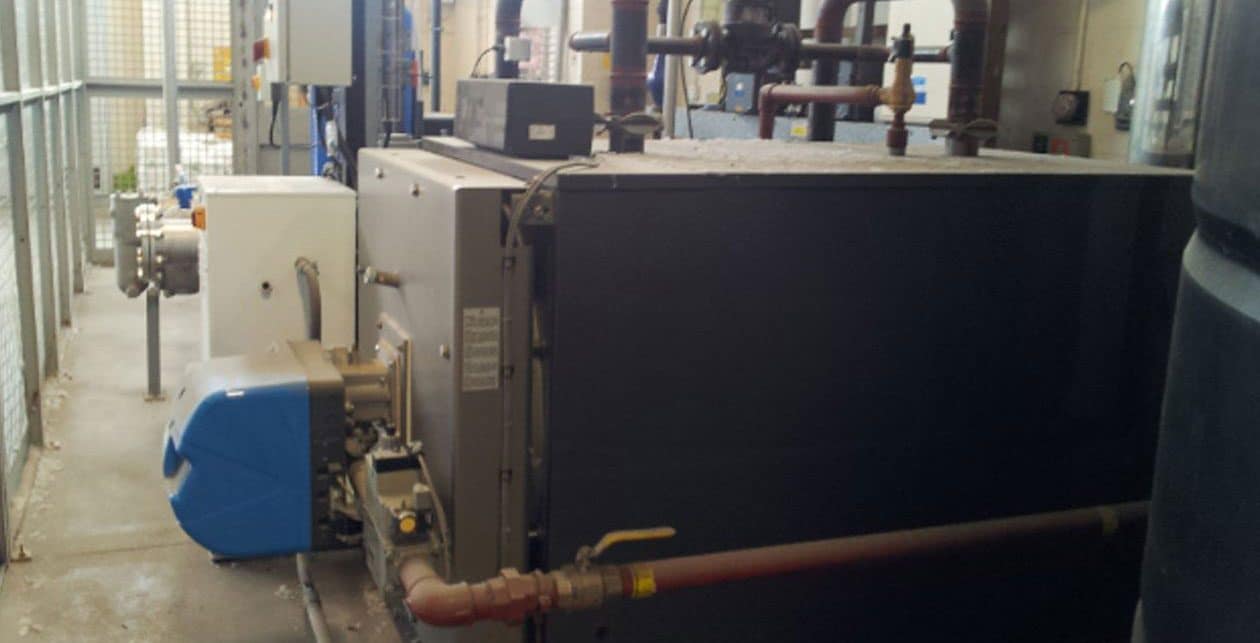
Plastics recycling firm Jayplas (J&A Young) has installed a Babcock Wanson HEB 420 Hot Water Boiler and Heat Exchanger into its latest recycling facility in Loughborough, Leicestershire.

Boilers for Plastic Recycling
The large-scale reprocessing facility has the capacity to process up to 25,000 tonnes per year of low density polyethylene film (LDPE) and is believed to be among the largest of its kind in the UK. Material for the plant includes back-of-store film waste from retailers, post-consumer polyethylene and plastic films from agricultural and construction sources. These are reprocessed into a plastic granulate for use in the production of new plastic film products, including refuse sacks and carrier bags.
In line with Jayplas’ philosophy to invest in technology that enables the company’s recycling plants to operate in an efficient and environmental way, the Babcock Wanson HEB 420 Hot Water Boiler was chosen by Jayplas for its high efficiency – up to 96.2% - and long working life.
HEB 420 Hot Water Boiler and Heat Exchanger
Babcock Wanson’s HEB Hot Water Boiler is a forced-circulation, fully automatic, gas, oil, dual fuel and / or biogas fired packaged unit with low emissions and high combustion efficiency specifically matched to the boiler. The reverse flame design provides optimum furnace loading and the radial firetube assembly minimises material stresses. The design of the combustion chamber and heat exchange surfaces has been optimised to suit the flame geometry of the matched burner. An easily reversible front door allows simple and quick access for inspection of the combustion chamber and reversal tubes without the need to remove the burner.
Jayplas is a long standing Babcock Wanson customer, employing a range of equipment. Commenting on this latest contract, Jason Hall, Group Engineering Manager, stated: “Jayplas was pleased to give this second project to Babcock Wanson with confidence due to the reliability of the ESM Steam Generator installed at our Corby site PET washing plant in 2010”.
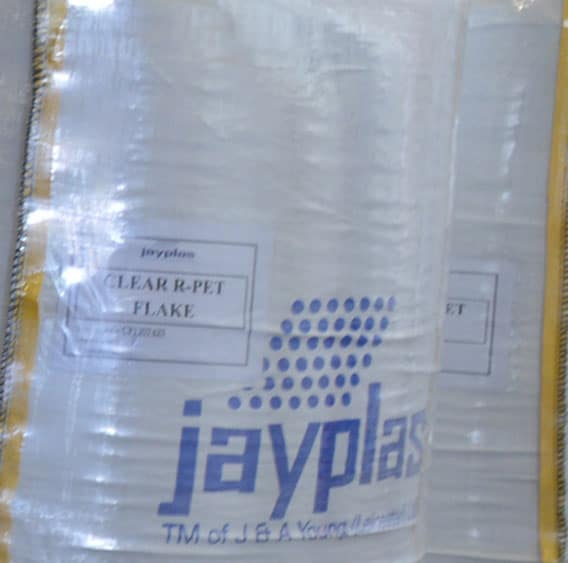
Customer Testimonials
— Loucas Antoniou, Engineering Manager at Bakkavor Meals London“The Thermal Oxidiser is the most efficient way of removing any smells and it’s also very straightforward to use. We have been a customer of Babcock Wanson for many years and have always enjoyed a good service.”
— Carbon Trust Annual Report 2009/10“A major carbon footprint reduction will be achieved when the scheme currently in progress to change the main boiler fuel from heating oil to gas is completed in summer 2010. This £900k project will reduce our carbon emissions via energy usage by around 15% by removing the need to use heavy fuel oil, as the new boiler plant will use natural gas as its main fuel source.”
— Webster & Horsfall“What we hadn’t expected initially though is the level of control the new system provides us with; it’s amazing. It alerts us to any potential issues, is easy to maintain (no annual statutory inspection is required) and is quick to respond. All that and it doesn’t take up much room.”
— Peter Connolly, Production Engineer at Vacu-Lug“The ESM 2000 installation, together with an ongoing programme of process plant lagging and steam trap maintenance, has enabled us to significantly reduce our gas usage and cushion the company against rising gas prices.”
— Dave Scrivens, Facilities Manager at Plastic Omnium“Babcock Wanson’s expertise and ability to provide a whole package made them the leading contender for this project. On further investigation, their proposal was also commercially viable, which sealed the deal.”
— Denis Kelly, Engineering & Construction Manager at Stolthaven Dagenham“The Thermal Fluid Heaters themselves were ideal for this project as they are based on mature technology and are well proven in the field. They are robust and also require very little maintenance.”
— Ian McQuarrie, Engineering Manager at Puredrive“During my three years here, the Steam Generators and Thermal Fluid Heaters have worked flawlessly. Babcock Wanson carries a good name in the business for both quality and equipment longevity. Their knowledge, company wide, is exceptional and the whole package from installation through to service is managed professionally.”
— Jason Hall, J&A Young Engineering Manager“We had estimated our steam requirements, but Babcock Wanson had the experience to understand that we had underestimated this. In fact, the erratic nature of the steam loads would have been impossible to meet under our existing spec. Babcock Wanson was able to identify this as well as provide a very energy efficient solution with a number of enhanced features”.
— Lee Bullen, Corrugated Services Manager at Board24“It’s running very well, both easy to use and efficient. The service from Babcock Wanson has also been very good.”
— Peter Shrimpton, Engineering Projects Manager at Bridgnorth Aluminium Ltd"We were unfamiliar with Babcock Wanson, but we’ve had no problems with it whatsoever; you simply switch it on and it works – simple as that! The service we have received from Babcock Wanson has also been great.”
You must be logged in to post a comment.