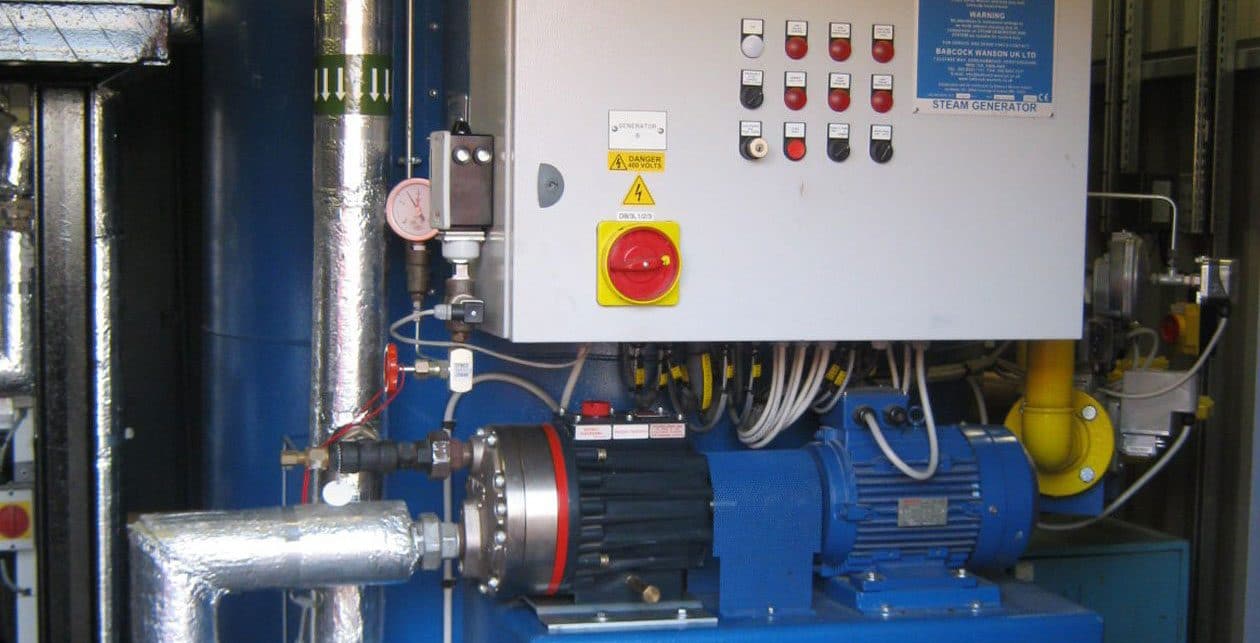
Babcock Wanson has supplied two 2000kg/h VPX Rapid Steam Generators to Martindale Pharma, a market leader in the manufacture and supply of specialty pharmaceuticals and services for healthcare professionals worldwide.
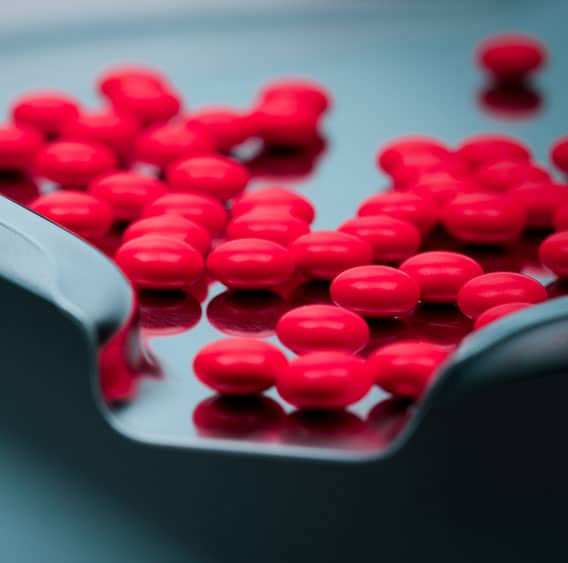
Steam Generators for Pharmaceutical Manufacturing
The two Steam Generators have been installed at Martindale Pharma’s principle site of manufacture in Romford, Essex, which specialises in the production of sterile ampoules, sterile screw cap bottles, non-sterile liquids, non-sterile suspensions and suppositories.
Steam is produced for a wide variety of uses across the Romford site, including the manufacturing production processes, production of Water for Injection (WFI) and a Pure Steam Generator (PSG), as well as heating for the company’s Air Handling Systems. The new VPX units have replaced four smaller generators that were unable to meet Martindale Pharma’s growth and subsequent capacity requirements.VPX Vertical Coil Steam Generators
VPX vertical coil Steam Generators from Babcock Wanson feature three full gas passes plus an in-built combustion air pre heater to give high operating efficiency. With availability of steam from cold start in as little as three minutes and a low volume of water under pressure the VPX Steam Generator combines efficiency with safety, even at very high working pressure. They are rugged in construction and very compact.
The pressure containing coil design of the VPX Steam Generator forms the main combustion chamber with the second and third passes for the gasses going between the coil windings to ensure high gas velocity with good heat transfer and self cleaning of the smoke side. Accurate flame dimensions are important for any combustion device and the use of a purpose built and matched Babcock Wanson burner ensures long life and simple operation. The feed water system is simple in operation and easy to maintain, consisting of either a multi diaphragm type positive displacement pump driven from an inverter controlled motor for both accurate control and lowest electrical demand.
As there is no discernible water level with a coil type boiler, the need for water level gauge glasses and other devices normally associated with fire tube boilers is eliminated with the associated reduction in boiler house manning demands. This equals simple and safe operation at the lowest practicable operating cost.
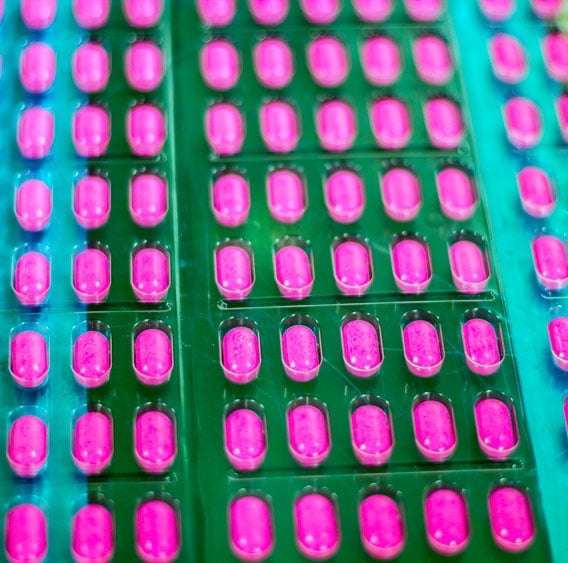
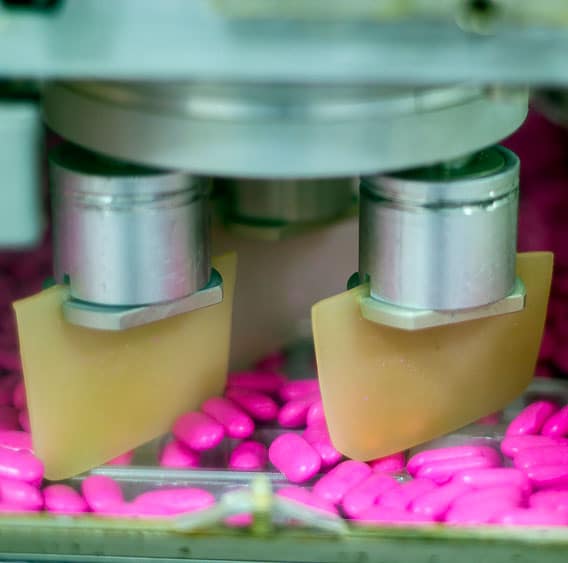
More than just an Installation
To maintain the Steam Generators’ efficiency and maximise their working life, Martindale Pharma has signed up to Babcock Wanson’s Water Treatment Service operated in conjunction with water treatment specialist Deep Water Blue. Under this service Martindale Pharma benefits from the deployment of highly qualified, professional chemists who ensure the treatment and testing regime is completed to obtain an accurate picture of the site’s specific requirements under a variety of conditions; this ensures the most appropriate chemical dosing regime is always employed. In between scheduled consultancy visits the unique vSteam® web portal allows Martindale Pharma to simply enter daily readings on-line and receive real-time feedback support.
Mark McLean, Engineering Team Leader at Martindale Pharma, is very pleased with the service; “the service from Deep Water Blue has so far been really good and the internet based reporting system is a fantastic tool for daily feedback on the water conditions, with instant advice on what to do to rectify any reading starting to drift out of specification.”
In addition, the Babcock Wanson Water Treatment Service provides a five year corrosion warranty on the steam generator coil. In the unlikely event of feed water deficiencies causing the coil to corrode within the first five years, Babcock Wanson will replace it under warranty.Customer Testimonials
— Loucas Antoniou, Engineering Manager at Bakkavor Meals London“The Thermal Oxidiser is the most efficient way of removing any smells and it’s also very straightforward to use. We have been a customer of Babcock Wanson for many years and have always enjoyed a good service.”
— Carbon Trust Annual Report 2009/10“A major carbon footprint reduction will be achieved when the scheme currently in progress to change the main boiler fuel from heating oil to gas is completed in summer 2010. This £900k project will reduce our carbon emissions via energy usage by around 15% by removing the need to use heavy fuel oil, as the new boiler plant will use natural gas as its main fuel source.”
— Webster & Horsfall“What we hadn’t expected initially though is the level of control the new system provides us with; it’s amazing. It alerts us to any potential issues, is easy to maintain (no annual statutory inspection is required) and is quick to respond. All that and it doesn’t take up much room.”
— Peter Connolly, Production Engineer at Vacu-Lug“The ESM 2000 installation, together with an ongoing programme of process plant lagging and steam trap maintenance, has enabled us to significantly reduce our gas usage and cushion the company against rising gas prices.”
— Dave Scrivens, Facilities Manager at Plastic Omnium“Babcock Wanson’s expertise and ability to provide a whole package made them the leading contender for this project. On further investigation, their proposal was also commercially viable, which sealed the deal.”
— Denis Kelly, Engineering & Construction Manager at Stolthaven Dagenham“The Thermal Fluid Heaters themselves were ideal for this project as they are based on mature technology and are well proven in the field. They are robust and also require very little maintenance.”
— Ian McQuarrie, Engineering Manager at Puredrive“During my three years here, the Steam Generators and Thermal Fluid Heaters have worked flawlessly. Babcock Wanson carries a good name in the business for both quality and equipment longevity. Their knowledge, company wide, is exceptional and the whole package from installation through to service is managed professionally.”
— Jason Hall, J&A Young Engineering Manager“We had estimated our steam requirements, but Babcock Wanson had the experience to understand that we had underestimated this. In fact, the erratic nature of the steam loads would have been impossible to meet under our existing spec. Babcock Wanson was able to identify this as well as provide a very energy efficient solution with a number of enhanced features”.
— Lee Bullen, Corrugated Services Manager at Board24“It’s running very well, both easy to use and efficient. The service from Babcock Wanson has also been very good.”
— Peter Shrimpton, Engineering Projects Manager at Bridgnorth Aluminium Ltd“We were unfamiliar with Babcock Wanson, but we’ve had no problems with it whatsoever; you simply switch it on and it works – simple as that! The service we have received from Babcock Wanson has also been great.”