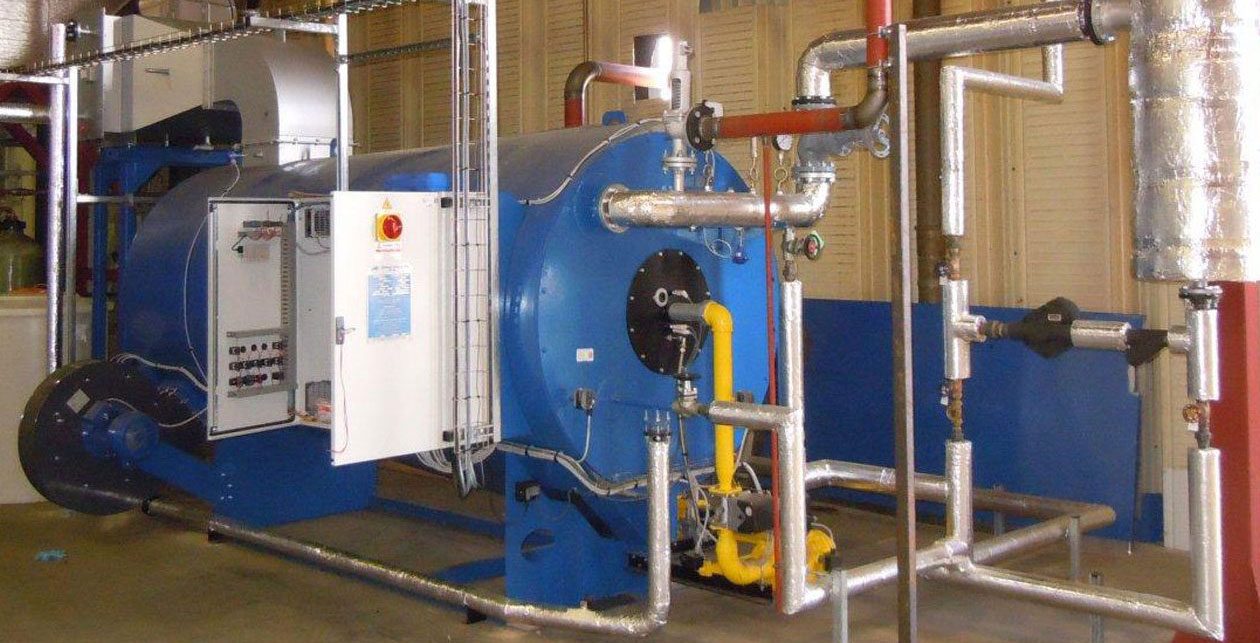
The UK’s largest plastic recycling company, J&A Young (Leicester) Ltd. has installed a Babcock Wanson ESM Steam Generator at its new recycling facility in Corby.

Steam Generation for Plastic Recycling
J&A Young’s first food-grade PET (Polyethylene terephthalate) recycling plant, with the ability to handle up to 30,000 tonnes of PET plastic bottles per annum, requires considerable amounts of steam to heat water as part of the recycling process. PET is used extensively for the production of bottles and other containers for the food industry so the need for an efficient re-cycling process has never been greater.
When looking at the options for generating steam, J&A Young Engineering Manager Jason Hall approached four companies but chose Babcock Wanson as they gave him the most confidence in their knowledge and skills. “We had estimated our steam requirements,” states Jason, “but Babcock Wanson had the experience to understand that we had underestimated this. In fact, the erratic nature of the steam loads would have been impossible to meet under our existing spec. Babcock Wanson was able to identify this as well as provide a very energy efficient solution with a number of enhanced features”.
ESM4000 Steam Generator
Babcock Wanson recommended its ESM4000 steam generator complete with exhaust gas recuperator for the feed water system plus an additional heat exchanger between the hot well and the feed pumps to further improve overall efficiency. A coil type steam generator, the ESM provides operating efficiencies of circa 96-97% overall and low emissions. It utilises modern controls to maintain a close ratio between the burner firing rate and water input with inverter drive of both the combustion air and feed water pumps. This ensures close control of both steam output and steam quality and lowest practicable consumption of electrical power.
The benefits of using high efficiency steam generators not only include energy consumption and carbon emissions but also improved safety (the chance of a pressurised water explosion is virtually eliminated), simplicity of control, compact size (they take about half the footprint of the previous fire tube boilers) and they are considerably quieter, cleaner and cooler in operation, making the boiler house a far nicer environment in which to work.
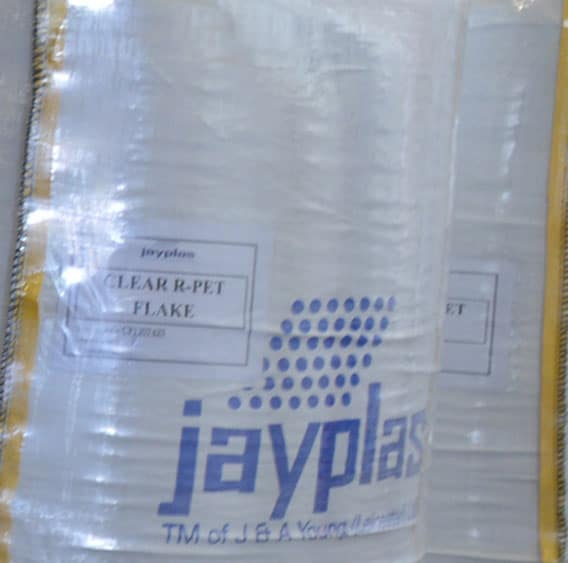
Customer Testimonials
— Loucas Antoniou, Engineering Manager at Bakkavor Meals London“The Thermal Oxidiser is the most efficient way of removing any smells and it’s also very straightforward to use. We have been a customer of Babcock Wanson for many years and have always enjoyed a good service.”
— Carbon Trust Annual Report 2009/10“A major carbon footprint reduction will be achieved when the scheme currently in progress to change the main boiler fuel from heating oil to gas is completed in summer 2010. This £900k project will reduce our carbon emissions via energy usage by around 15% by removing the need to use heavy fuel oil, as the new boiler plant will use natural gas as its main fuel source.”
— Webster & Horsfall“What we hadn’t expected initially though is the level of control the new system provides us with; it’s amazing. It alerts us to any potential issues, is easy to maintain (no annual statutory inspection is required) and is quick to respond. All that and it doesn’t take up much room.”
— Peter Connolly, Production Engineer at Vacu-Lug“The ESM 2000 installation, together with an ongoing programme of process plant lagging and steam trap maintenance, has enabled us to significantly reduce our gas usage and cushion the company against rising gas prices.”
— Dave Scrivens, Facilities Manager at Plastic Omnium“Babcock Wanson’s expertise and ability to provide a whole package made them the leading contender for this project. On further investigation, their proposal was also commercially viable, which sealed the deal.”
— Denis Kelly, Engineering & Construction Manager at Stolthaven Dagenham“The Thermal Fluid Heaters themselves were ideal for this project as they are based on mature technology and are well proven in the field. They are robust and also require very little maintenance.”
— Ian McQuarrie, Engineering Manager at Puredrive“During my three years here, the Steam Generators and Thermal Fluid Heaters have worked flawlessly. Babcock Wanson carries a good name in the business for both quality and equipment longevity. Their knowledge, company wide, is exceptional and the whole package from installation through to service is managed professionally.”
— Jason Hall, J&A Young Engineering Manager“We had estimated our steam requirements, but Babcock Wanson had the experience to understand that we had underestimated this. In fact, the erratic nature of the steam loads would have been impossible to meet under our existing spec. Babcock Wanson was able to identify this as well as provide a very energy efficient solution with a number of enhanced features”.
— Lee Bullen, Corrugated Services Manager at Board24“It’s running very well, both easy to use and efficient. The service from Babcock Wanson has also been very good.”
— Peter Shrimpton, Engineering Projects Manager at Bridgnorth Aluminium Ltd"We were unfamiliar with Babcock Wanson, but we’ve had no problems with it whatsoever; you simply switch it on and it works – simple as that! The service we have received from Babcock Wanson has also been great.”
You must be logged in to post a comment.